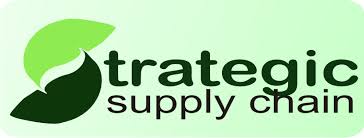
Lean manufacturing, a management method that helps to reduce waste and increase efficiency, is what it stands for. It's based on the principles of Henry Ford and KiichiroToyoda who were the presidents of Toyota Motor Corporation before World War II. In lean, manufacturing is considered a whole system, not just an assembly line. There are five key principles of lean: eliminate waste, streamline the process, create knowledge, optimize the whole, and use continuous improvement.
It is important to first identify what you are doing wrong. This can be done with quantitative or qualitative techniques. You can check the price that your customers pay for your product. If the price you charge is more than the value that you provide, then you may have a problem.
Kaizen events are a great way to assess the amount waste in a process. This involves everyone in the organization working together to solve problems on an incremental basis. Kaizen events are a combination of other lean tools and can be used by themselves or with others.
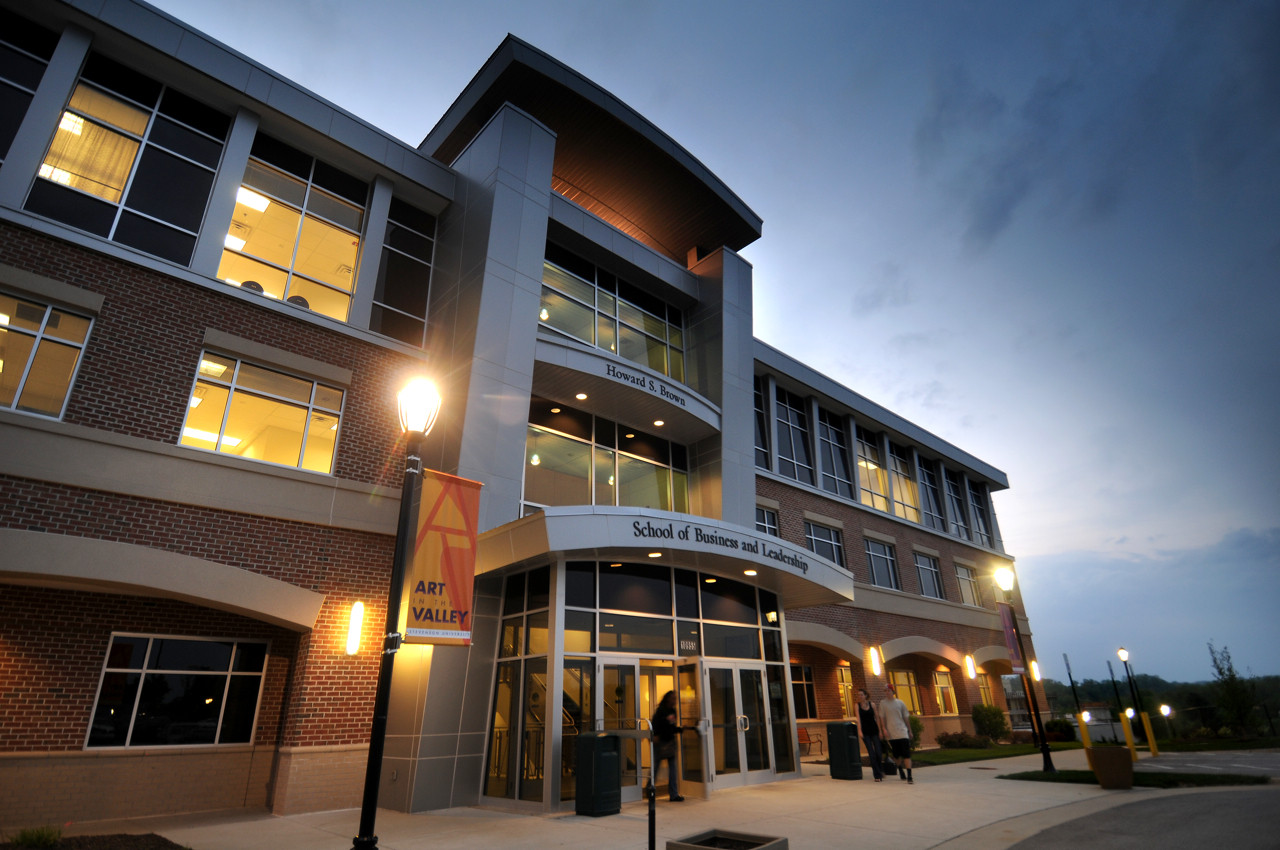
Value stream mapping is another way to identify production waste. VSM is a way for manufacturers to see the production steps and determine which are the most time-consuming.
Inventory, waiting and overproduction are all waste areas. A lean team will map out these areas to identify where improvements can be made. They can be found in the supply chains, in the production areas, or throughout the entire process.
After identifying the waste, you are able to start implementing strategies for eliminating it. These include developing cross-functional teams, flattening your workload, and training your employees to be multi-skilled. Depending on your business, you may want to implement technologies like just-in-time or cellular manufacturing. You can also utilize other lean tools such total productive maintenance or kanban administration.
It is possible to incorporate a system with standardized containers. This allows workers to determine exact quantities without having to count. It is easier to determine if food, or other substances are mixed into the products using standardized containers. Safety mats can also be placed near machine areas to trigger a stoppage if a person steps on them.
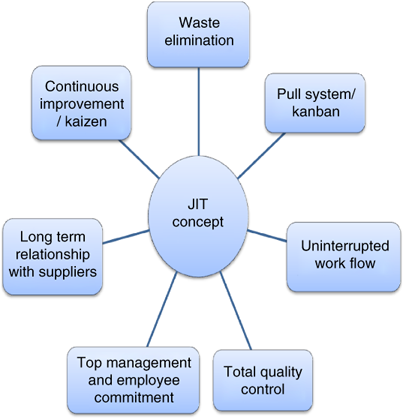
You will need to have a strong organizational culture, as with all lean initiatives. That culture should include an understanding of what the goal of the initiative is, communication skills, and a long-term focus. A sustainable system of improvement is essential to the success of your business.
When you're looking at a new machine, value stream mapping is a great tool. You can create an inventory that includes the future condition of your products, raw materials, and customer needs. This information allows you to more accurately predict when and how much equipment you will need. A scheduling system can be created to help you meet your orders on time.
You can increase your company's efficiency and help you reach your goals by incorporating five key principles of lean production. You can learn more about the techniques and resources available to you at various lean manufacturing websites.
FAQ
What are the 7 Rs of logistics management?
The acronym 7Rs of Logistics refers to the seven core principles of logistics management. It was developed by the International Association of Business Logisticians (IABL) and published in 2004 as part of its "Seven Principles of Logistics Management" series.
The following letters make up the acronym:
-
Responsible - to ensure that all actions are within the legal requirements and are not detrimental to others.
-
Reliable – have faith in your ability and capability to keep promises.
-
Reasonable - make sure you use your resources well and don't waste them.
-
Realistic – consider all aspects of operations, from cost-effectiveness to environmental impact.
-
Respectful - Treat people fairly and equitably
-
Responsive - Look for ways to save time and increase productivity.
-
Recognizable - provide customers with value-added services.
What is the job of a production plan?
Production planners ensure all aspects of the project are delivered within time and budget. They also ensure that the product/service meets the client’s needs.
What is production planning?
Production Planning involves developing a plan for all aspects of the production, including scheduling, budgeting, casting, crew, location, equipment, props, etc. This document is designed to make sure everything is ready for when you're ready to shoot. This document should include information about how to achieve the best results on-set. This includes information on shooting times, locations, cast lists and crew details.
First, you need to plan what you want to film. You may have decided where to shoot or even specific locations you want to use. Once you have determined your scenes and locations, it is time to start figuring out the elements that you will need for each scene. You might decide you need a car, but not sure what make or model. If this is the case, you might start searching online for car models and then narrow your options by selecting from different makes.
After you have chosen the right car, you will be able to begin thinking about accessories. What about additional seating? Perhaps you have someone who needs to be able to walk around the back of your car. You might want to change your interior color from black and white. These questions will help you determine the exact look and feel of your car. You can also think about the type of shots you want to get. What type of shots will you choose? Perhaps you want to show the engine or the steering wheel? These things will help you to identify the car that you are looking for.
Once you have established all the details, you can create a schedule. You can create a schedule that will outline when you must start and finish your shoots. Each day will include the time when you need to arrive at the location, when you need to leave and when you need to return home. Everyone will know what they need and when. You can also make sure to book extra staff in advance if you have to hire them. You should not hire anyone who doesn't show up because of your inaction.
Your schedule will also have to be adjusted to reflect the number of days required to film. Some projects take only a few days while others can last several weeks. It is important to consider whether you require more than one photo per day when you create your schedule. Multiple takes of the same location will lead to higher costs and take more time. If you aren't sure whether you need multiple shots, it is best to take fewer photos than you would like.
Another important aspect of production planning is setting budgets. Setting a realistic budget is essential as it will allow you to work within your means. Remember that you can always reduce the budget later on if you run into unforeseen problems. You shouldn't underestimate the amount you'll spend. You'll end up with less money after paying for other things if the cost is underestimated.
Production planning is a detailed process. But, once you understand the workings of everything, it becomes easier for future projects to be planned.
How can we increase manufacturing efficiency?
The first step is to determine the key factors that impact production time. The next step is to identify the most important factors that affect production time. If you don’t know where to begin, consider which factors have the largest impact on production times. Once you've identified them all, find solutions to each one.
What is meant by manufacturing industries?
Manufacturing Industries are companies that manufacture products. Consumers are the people who purchase these products. To accomplish this goal, these companies employ a range of processes including distribution, sales, management, and production. They create goods from raw materials, using machines and various other equipment. This covers all types of manufactured goods including clothing, food, building supplies and furniture, as well as electronics, tools, machinery, vehicles and pharmaceuticals.
What jobs are available in logistics?
There are many jobs available in logistics. Some of them are:
-
Warehouse workers – They load and unload pallets and trucks.
-
Transportation drivers – These drivers drive trucks and wagons to transport goods and pick up the goods.
-
Freight handlers: They sort and package freight in warehouses.
-
Inventory managers – They manage the inventory in warehouses.
-
Sales representatives - They sell products to customers.
-
Logistics coordinators – They plan and coordinate logistics operations.
-
Purchasing agents – They buy goods or services necessary to run a company.
-
Customer service representatives - They answer calls and emails from customers.
-
Shipping clerks: They process shipping requests and issue bills.
-
Order fillers - They fill orders based on what is ordered and shipped.
-
Quality control inspectors - They check incoming and outgoing products for defects.
-
Others - There are many other types of jobs available in logistics, such as transportation supervisors, cargo specialists, etc.
Statistics
- You can multiply the result by 100 to get the total percent of monthly overhead. (investopedia.com)
- According to the United Nations Industrial Development Organization (UNIDO), China is the top manufacturer worldwide by 2019 output, producing 28.7% of the total global manufacturing output, followed by the United States, Japan, Germany, and India.[52][53] (en.wikipedia.org)
- In the United States, for example, manufacturing makes up 15% of the economic output. (twi-global.com)
- Job #1 is delivering the ordered product according to specifications: color, size, brand, and quantity. (netsuite.com)
- It's estimated that 10.8% of the U.S. GDP in 2020 was contributed to manufacturing. (investopedia.com)
External Links
How To
How to Use the Just In Time Method in Production
Just-intime (JIT), which is a method to minimize costs and maximize efficiency in business process, is one way. It's a way to ensure that you get the right resources at just the right time. This means that you only pay for what you actually use. Frederick Taylor, a 1900s foreman, first coined the term. He observed how workers were paid overtime if there were delays in their work. He concluded that if workers were given enough time before they start work, productivity would increase.
JIT is an acronym that means you need to plan ahead so you don’t waste your money. The entire project should be looked at from start to finish. You need to ensure you have enough resources to tackle any issues that might arise. You'll be prepared to handle any potential problems if you know in advance. This will prevent you from spending extra money on unnecessary things.
There are many JIT methods.
-
Demand-driven JIT: You order the parts and materials you need for your project every other day. This will allow for you to track the material that you have left after using it. It will also allow you to predict how long it takes to produce more.
-
Inventory-based: This allows you to store the materials necessary for your projects in advance. This allows one to predict how much they will sell.
-
Project-driven: This method allows you to set aside enough funds for your project. When you know how much you need, you'll purchase the appropriate amount of materials.
-
Resource-based JIT: This is the most popular form of JIT. Here you can allocate certain resources based purely on demand. You will, for example, assign more staff to deal with large orders. If you don't have many orders, you'll assign fewer people to handle the workload.
-
Cost-based: This is a similar approach to resource-based but you are not only concerned with how many people you have, but also how much each one costs.
-
Price-based: This is very similar to cost-based, except that instead of looking at how much each individual worker costs, you look at the overall price of the company.
-
Material-based: This approach is similar to cost-based. However, instead of looking at the total cost for the company, you look at how much you spend on average on raw materials.
-
Time-based: This is another variation of resource-based JIT. Instead of focusing only on how much each employee is costing, you should focus on how long it takes to complete your project.
-
Quality-based JIT is another variant of resource-based JIT. Instead of focusing on the cost of each worker or how long it takes, think about how high quality your product is.
-
Value-based JIT: This is the latest form of JIT. In this scenario, you're not concerned about how products perform or whether customers expect them to meet their expectations. Instead, you focus on the added value that you provide to your market.
-
Stock-based: This is an inventory-based method that focuses on the actual number of items being produced at any given time. It's used when you want to maximize production while minimizing inventory.
-
Just-in-time planning (JIT): This is a combination JIT and supply-chain management. It is the process that schedules the delivery of components within a short time of their order. It is essential because it reduces lead-times and increases throughput.