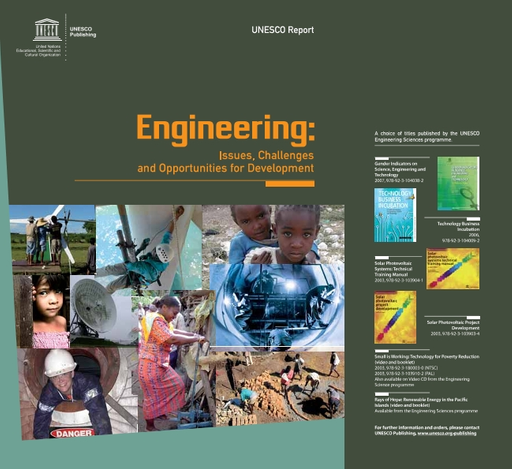
Managing a supply chain involves several aspects of a firm. This includes both internal processes and the flow and distribution of finished goods and information. Marketing includes supply chain management. In almost all industries, supply chains are utilized. The primary function of the supply chains is to deliver products to customers. It is an objective of the supply chain to deliver products in a timely manner.
A person responsible for overseeing business processes is called an operations manager. This includes the supervision of staffing and hiring. They also manage production and plan. They will also be responsible for creating a strategy that will improve operations. The operations manager has to ensure sufficient inventory for production, budget compliance, and conformance with company specifications. He coordinates with the supply chain manager to ship orders to retailers and consumers.
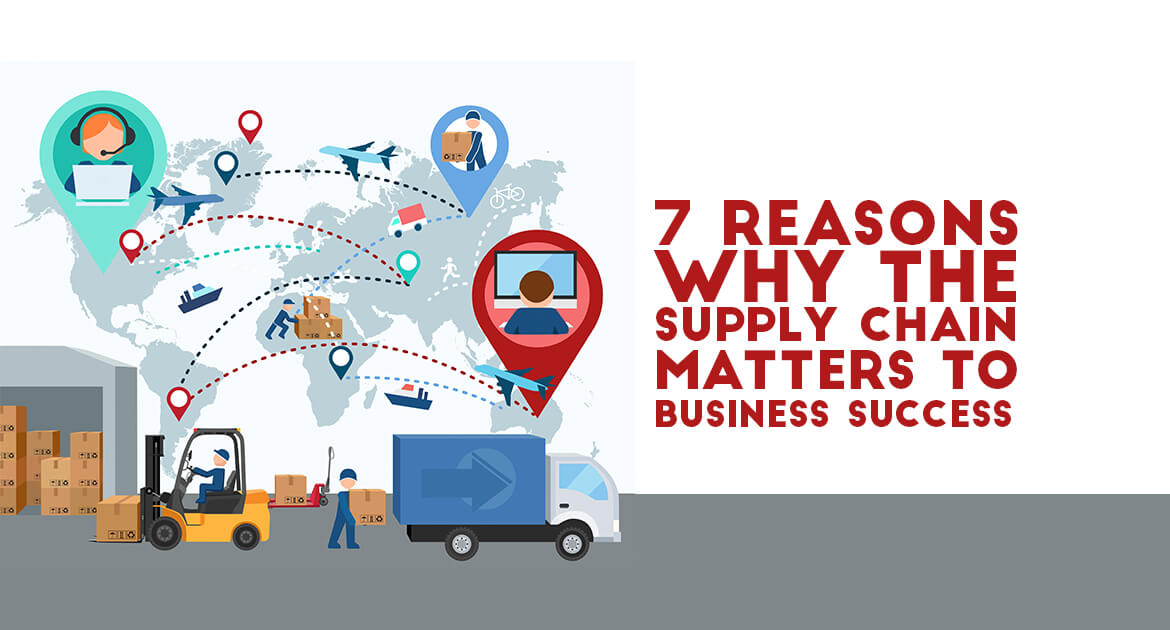
The operations and supply chains program at UTSA is designed for you to enhance your leadership and analytical skills. The program is hands-on and combines classroom instruction with experiential learning. The program offers data analysis skills, business process improvement, green belt certification in Lean Six Sigma, and Lean Six Sigma. The program provides an overview of supply chain operations and offers a detailed view. You will also have the opportunity to learn new technologies and apply them to your business.
The Operations and Supply Chain program is designed to focus on value-adding process. The program provides students with the skills they need to make better business decisions. This program is based on a range of industrial cases and case studies. It also teaches students how communicate effectively and to use computers. A minor is also offered in this program. The minor is designed as a complement to the major and to enhance students' ability to optimize their supply chain. The minor can be taken as either a Contexts and Perspectives course or unrestricted elective.
Students have the chance to gain valuable knowledge about operations and supply chain. Students also have the unique opportunity to apply concepts to their own businesses. It can be used to help you get into management, marketing, or technology. It also allows students to apply for the Lean Six Sigma green belt certification. You can also interact with industry professionals and learn new technologies and trends.
Students will also have the opportunity to learn about the production and distribution of products and services in the operations and supply chains program. It also teaches students the skills of communication, which are essential in business and managerial management.
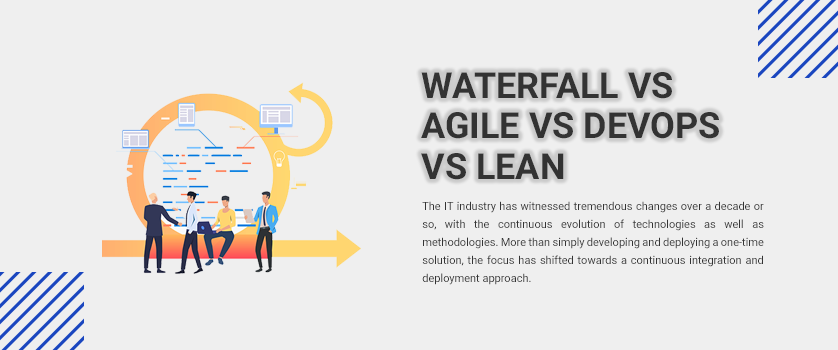
It's written in a very user-friendly way. The book is accessible to students of all backgrounds. In addition to describing how the supply chain works, the book presents a number of case studies, and discusses how to design a supply network. The book also explains quantitative methods for comparing demand and supply. It also describes how to incorporate customers into your supply-chain.
FAQ
What are manufacturing & logistics?
Manufacturing is the production of goods using raw materials. Logistics includes all aspects related to supply chain management, such as procurement, distribution planning, inventory control and transportation. Sometimes manufacturing and logistics are combined to refer to a wider term that includes both the process of creating products as well as their delivery to customers.
Why automate your warehouse?
Modern warehousing is becoming more automated. With the rise of ecommerce, there is a greater demand for faster delivery times as well as more efficient processes.
Warehouses must be able to quickly adapt to changing demands. They must invest heavily in technology to do this. Automation warehouses can bring many benefits. Here are some of the reasons automation is worth your investment:
-
Increases throughput/productivity
-
Reduces errors
-
Increases accuracy
-
Safety Boosts
-
Eliminates bottlenecks
-
Companies can scale more easily
-
Makes workers more efficient
-
Provides visibility into everything that happens in the warehouse
-
Enhances customer experience
-
Improves employee satisfaction
-
Reduces downtime and improves uptime
-
You can be sure that high-quality products will arrive on time
-
Eliminates human error
-
It helps ensure compliance with regulations
What is production planning?
Production planning is the process of creating a plan that covers all aspects of production. This includes scheduling, budgeting and crew, location, equipment, props, and more. This document is designed to make sure everything is ready for when you're ready to shoot. You should also have information to ensure the best possible results on set. It should include information about shooting locations, casting lists, crew details, equipment requirements, and shooting schedules.
It is important to first outline the type of film you would like to make. You may have already decided where you would like to shoot, or maybe there are specific locations or sets that you want to use. Once you have identified the scenes and locations, you can start to determine which elements are required for each scene. You might decide you need a car, but not sure what make or model. If this is the case, you might start searching online for car models and then narrow your options by selecting from different makes.
After you've found the perfect car, it's time to start thinking about adding extras. Are you looking for people to sit in the front seats? You might also need someone to help you get around the back. You may want to change the interior's color from black or white. These questions will help guide you in determining the ideal look and feel for your car. Another thing you can do is think about what type of shots are desired. What type of shots will you choose? Maybe you want to show the engine and the steering wheel. All of these things will help you identify the exact style of car you want to film.
Once you have made all the necessary decisions, you can start to create a schedule. You can create a schedule that will outline when you must start and finish your shoots. A schedule for each day will detail when you should arrive at the location and when you need leave. This way, everyone knows what they need to do and when. If you need to hire extra staff, you can make sure you book them in advance. It is not worth hiring someone who won’t show up because you didn’t tell him.
Also, consider how many days you will be filming your schedule. Some projects are quick and easy, while others take weeks. When you are creating your schedule, you should always keep in mind whether you need more than one shot per day or not. Multiplying takes in the same area will result both in increased costs and a longer time. If you aren't sure whether you need multiple shots, it is best to take fewer photos than you would like.
Budget setting is another important aspect in production planning. A realistic budget will help you work within your means. Remember that you can always reduce the budget later on if you run into unforeseen problems. It is important to not overestimate how much you will spend. Underestimating the cost will result in less money after you have paid for other items.
Production planning is a very detailed process, but once you understand how everything works together, it becomes easier to plan future projects.
What does manufacturing mean?
Manufacturing Industries is a group of businesses that produce goods for sale. The people who buy these products are called consumers. This is accomplished by using a variety of processes, including production, distribution and retailing. They produce goods from raw materials by using machines and other machinery. This includes all types if manufactured goods.
Statistics
- In 2021, an estimated 12.1 million Americans work in the manufacturing sector.6 (investopedia.com)
- In the United States, for example, manufacturing makes up 15% of the economic output. (twi-global.com)
- Many factories witnessed a 30% increase in output due to the shift to electric motors. (en.wikipedia.org)
- Job #1 is delivering the ordered product according to specifications: color, size, brand, and quantity. (netsuite.com)
- It's estimated that 10.8% of the U.S. GDP in 2020 was contributed to manufacturing. (investopedia.com)
External Links
How To
Six Sigma and Manufacturing
Six Sigma is "the application statistical process control (SPC), techniques for continuous improvement." Motorola's Quality Improvement Department in Tokyo, Japan developed Six Sigma in 1986. Six Sigma's core idea is to improve the quality of processes by standardizing and eliminating defects. In recent years, many companies have adopted this method because they believe there is no such thing as perfect products or services. Six Sigma's main objective is to reduce variations from the production average. This means that you can take a sample from your product and then compare its performance to the average to find out how often the process differs from the norm. If this deviation is too big, you know something needs fixing.
Understanding the nature of variability in your business is the first step to Six Sigma. Once you understand this, you can then identify the causes of variation. It is important to identify whether the variations are random or systemic. Random variations are caused by human errors. Systematic variations can be caused by outside factors. If you make widgets and some of them end up on the assembly line, then those are considered random variations. But if you notice that every widget you make falls apart at the exact same place each time, this would indicate that there is a problem.
After identifying the problem areas, you will need to devise solutions. The solution could involve changing how you do things, or redesigning your entire process. To verify that the changes have worked, you need to test them again. If they don't work you need to rework them and come up a better plan.