
Lean management is an effective way to reduce waste in the workplace. It is based upon the belief that all activities or processes in an organization should add value for its customers. This can be accomplished by eliminating all activities that do no add value and working systematically to create value.
A lean management is designed to increase the performance of an organization. It also helps ensure employees understand the purpose and goal of their work.
In lean system management, the first step is to determine what value is. It involves identifying the value that a customer is looking for and creating a solution to meet that need. This can be achieved by ensuring everything, from the manufacturing process to customer services is efficient and consistent.
The use of lean principles in the production of products can be an effective way to cut costs and increase efficiency. However, it is important to get your employees on board. The results of the program could be disastrous if the staff is not committed.
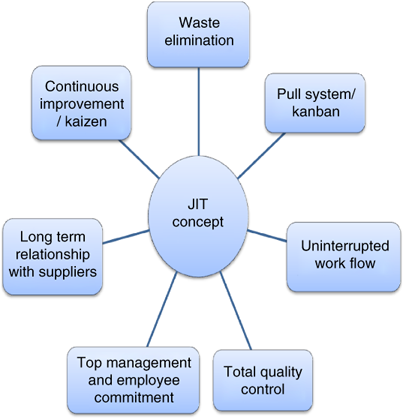
Along with gaining the buy-in of your workforce, it is important to ensure that you have a healthy supply network. Because most lean programs require significant retooling in the supply chain, it is important to get the right results.
You should ensure your staff are well-trained in lean principles. You can do this by making sure that your employees are aware of what waste is and the importance of removing it from production.
You should also take into account the need for teamwork when you implement lean principles. It can be difficult, but teamwork is an essential part of lean principles and will help eliminate wastes in your production line.
It will help your team produce higher quality products and improve your bottom line. You can encourage this by giving them a chance to meet with each other regularly and discuss ways to get rid of wastes in their work.
Lean managers will help you reach this goal by ensuring workers are trained properly and have the knowledge to implement these techniques. A lean manager can help keep your production process running smoothly by keeping everyone informed about any issues.
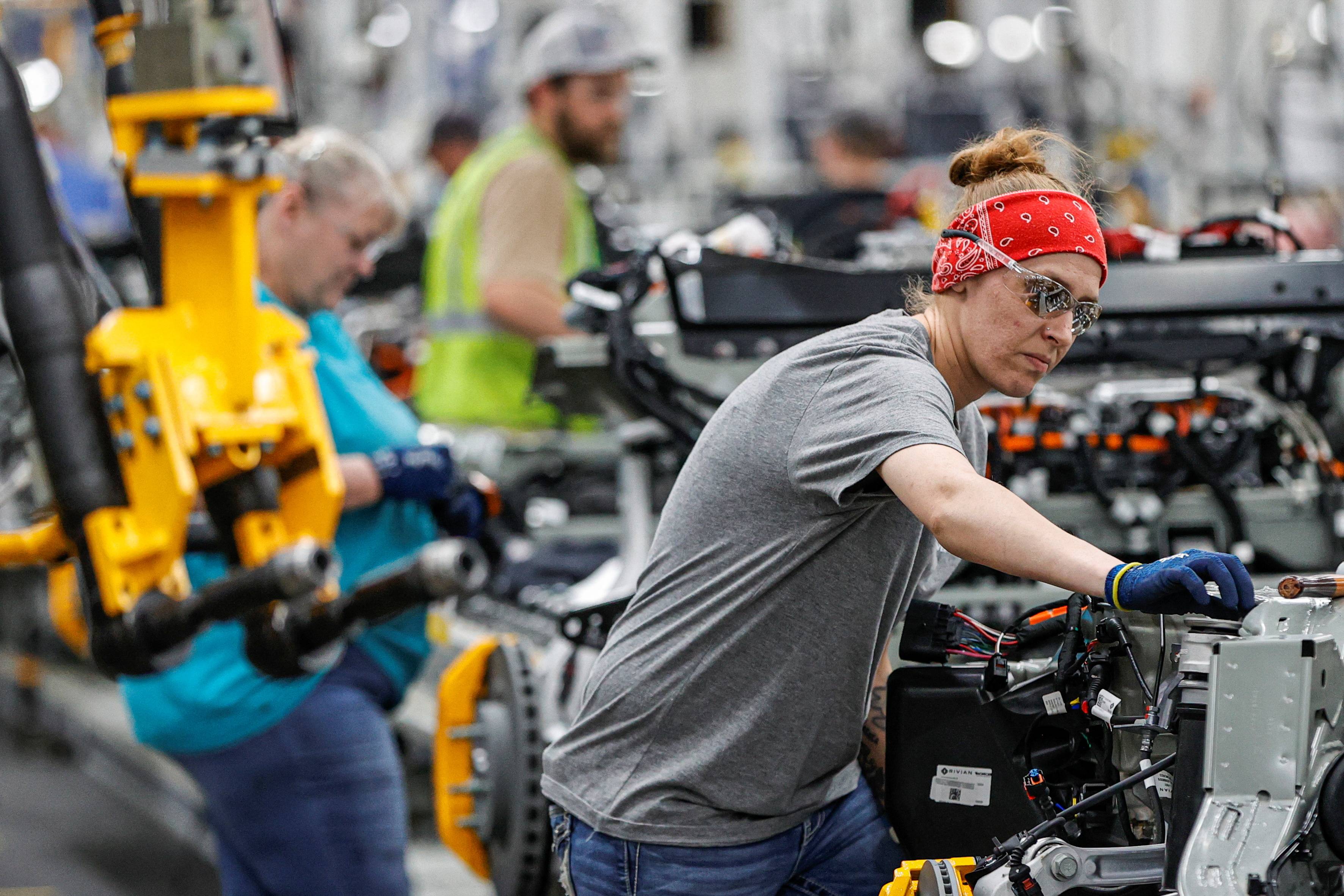
The final step in lean system management is to monitor and improve each of the procedures that are being implemented. This can be done by tracking the progress of each project as it is completed and ensuring that any changes that need to be made are implemented correctly.
According to the size of your company, you may have to hire someone to oversee your lean operations. If you search for jobs in lean management or look at job boards, you can find candidates who fit this role.
FAQ
What are manufacturing and logistic?
Manufacturing refers to the process of making goods using raw materials and machines. Logistics manages all aspects of the supply chain, including procurement, production planning and distribution, inventory control, transportation, customer service, and transport. Manufacturing and logistics can often be grouped together to describe a larger term that covers both the creation of products, and the delivery of them to customers.
What does warehouse refer to?
A warehouse is a place where goods are stored until they are sold. It can be either an indoor or outdoor space. It could be one or both.
How can manufacturing avoid production bottlenecks
To avoid production bottlenecks, ensure that all processes run smoothly from the moment you receive your order to the time the product ships.
This includes planning for capacity requirements as well as quality control measures.
Continuous improvement techniques like Six Sigma are the best way to achieve this.
Six Sigma management is a system that improves quality and reduces waste within your organization.
It is focused on creating consistency and eliminating variation in your work.
What's the difference between Production Planning & Scheduling?
Production Planning (PP) is the process of determining what needs to be produced at any given point in time. Forecasting and identifying production capacity are two key elements to this process.
Scheduling involves the assignment of dates and times to tasks in order to complete them within the timeframe.
What is the job of a logistics manger?
Logistics managers are responsible for ensuring that all goods arrive in perfect condition and on time. This is accomplished by using the experience and knowledge gained from working with company products. He/she also needs to ensure adequate stock to meet demand.
Statistics
- (2:04) MTO is a production technique wherein products are customized according to customer specifications, and production only starts after an order is received. (oracle.com)
- Many factories witnessed a 30% increase in output due to the shift to electric motors. (en.wikipedia.org)
- In the United States, for example, manufacturing makes up 15% of the economic output. (twi-global.com)
- According to a Statista study, U.S. businesses spent $1.63 trillion on logistics in 2019, moving goods from origin to end user through various supply chain network segments. (netsuite.com)
- [54][55] These are the top 50 countries by the total value of manufacturing output in US dollars for its noted year according to World Bank.[56] (en.wikipedia.org)
External Links
How To
How to Use Just-In-Time Production
Just-in time (JIT), is a process that reduces costs and increases efficiency in business operations. It allows you to get the right amount resources at the right time. This means you only pay what you use. Frederick Taylor was the first to coin this term. He developed it while working as a foreman during the early 1900s. He noticed that workers were often paid overtime when they had to work late. He decided to ensure workers have enough time to do their jobs before starting work to improve productivity.
JIT teaches you to plan ahead and prepare everything so you don’t waste time. You should also look at the entire project from start to finish and make sure that you have sufficient resources available to deal with any problems that arise during the course of your project. You'll be prepared to handle any potential problems if you know in advance. This way you won't be spending more on things that aren’t really needed.
There are several types of JIT techniques:
-
Demand-driven JIT: This is a JIT that allows you to regularly order the parts/materials necessary for your project. This will allow you to track how much material you have left over after using it. This will allow you to calculate how long it will take to make more.
-
Inventory-based: This type allows you to stock the materials needed for your projects ahead of time. This allows for you to anticipate how much you can sell.
-
Project-driven: This means that you have enough money to pay for your project. Once you have an idea of how much material you will need, you can purchase the necessary materials.
-
Resource-based JIT: This type of JIT is most commonly used. You allocate resources based on the demand. For example, if there is a lot of work coming in, you will have more people assigned to them. If you don’t have many orders you will assign less people to the work.
-
Cost-based : This is similar in concept to resource-based. But here, you aren't concerned about how many people your company has but how much each individual costs.
-
Price-based: This approach is very similar to the cost-based method except that you don't look at individual workers costs but the total cost of the company.
-
Material-based: This approach is similar to cost-based. However, instead of looking at the total cost for the company, you look at how much you spend on average on raw materials.
-
Time-based JIT is another form of resource-based JIT. Instead of focusing on how much each employee costs, you focus on how long it takes to complete the project.
-
Quality-based JIT: Another variation on resource-based JIT. Instead of worrying about the costs of each employee or how long it takes for something to be made, you should think about how quality your product is.
-
Value-based JIT: One of the most recent forms of JIT. In this case, you're not concerned with how well the products perform or whether they meet customer expectations. Instead, you are focused on adding value to the marketplace.
-
Stock-based: This is an inventory-based method that focuses on the actual number of items being produced at any given time. It's useful when you want maximum production and minimal inventory.
-
Just-intime planning (JIT), is a combination JIT/sales chain management. It's the process of scheduling delivery of components immediately after they are ordered. It is essential because it reduces lead-times and increases throughput.