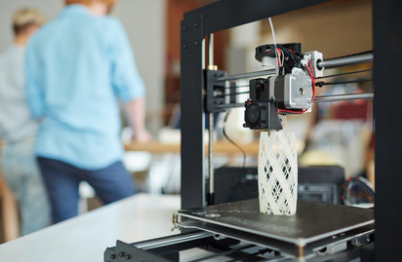
A chemical engineer is a professional with knowledge in the field of chemistry and engineering. They design and manage equipment and processes that transform raw materials into finished products. They oversee all aspects of the manufacturing process, from plant layouts and equipment operation to design. Regardless of your area of interest, a chemical engineering degree can be rewarding and lucrative. Here are some career options in the field. These professionals are an asset to any industry in which they work, including pharmaceuticals and food.
Aerospace engineering is one of the most difficult majors
This major in aerospace engineering requires high levels of discipline. This major doesn't allow for college party culture. You will be expected to spend hours learning and doing course-related work. This is often called rocket science. Aerospace engineering deals with the design and construction of spacecraft. It encompasses the overlap of aerospace engineering and astronautical. Students will need to study a heavy mathematical load, and fluid dynamics.
Chemical engineering is the easiest major
A high GPA in high school is a prerequisite for chemical engineering. Colleges expect chemical engineers to complete rigorous coursework in high school. Taking AP classes can make you stand out to admissions officers. AP classes also give students a solid academic foundation. Chemical engineers are highly-paid jobs with a median annual salary of $96,300 for 2020.
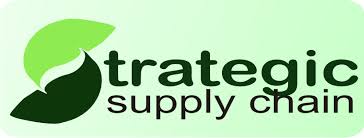
It involves math, physics, as well as chemistry.
Most undergraduate programs in chemical engineers require 120-130 credits and last four years. Students will learn how to design, fabricate, and analyze chemical products and processes, and develop manufacturing equipment. Chemical engineering students take classes in math, physics and chemistry. Students also participate in internships or cooperative learning. Some programs offer doctoral degrees. A bachelor's degree in chemical engineer is required to be eligible for a PhD.
It is a stable industry
There are many types of jobs available in chemical engineering. Many chemical engineers work in offices and laboratories, but they may also spend time on site, where they direct operations and solve problems. While they work long hours to meet deadlines. They might also be available at short notice. This field requires a deep understanding of complex topics. For example, a chemical engineering professional may use computer-aided modeling software to help design the best process.
It pays well
If you're a recent college graduate looking for an entry-level job, there are plenty of options available. If no position has been posted, you can look for an internship. Some companies, such as ExxonMobil, are hiring and may have positions available. Engineering, finance, operations and geoscience are all possible career options. Focus on your expertise in operations, geophysics or information technology.
It is a relatively recent subject
Chemistry engineering is fascinating and challenging. The many applications of chemical engineering are what you will learn as a student. You will learn how to design and build industrial processes with complex operations. Learn about unit operations in chemical plants as well as the consequences of changing the variables. Throughout the history of chemical engineering, innovative approaches have been implemented to improve student understanding and participation.
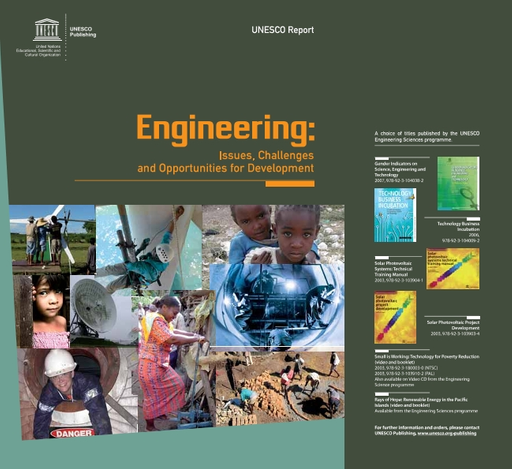
Students who are interested in this field will find it a great fit.
If you're interested to work in the chemical sector, there are many reasons for majoring in chemical engineer. In addition to developing specialist knowledge, this field also works alongside other disciplines such as electrical engineering. Chemical engineers have the ability to identify and solve problems in chemical manufacturing, use, transportation and distribution. Food, fuel, drugs and food are some of the chemicals produced today. Depending on your interests and expertise, you may choose to concentrate on particular sub-groups of the field such as biotechnology or environmental.
FAQ
What is production planning?
Production Planning is the creation of a plan to cover all aspects, such as scheduling, budgeting. Location, crew, equipment, props and other details. This document ensures that everything is prepared and available when you are ready for shooting. It should also contain information on achieving the best results on set. It should include information about shooting locations, casting lists, crew details, equipment requirements, and shooting schedules.
First, you need to plan what you want to film. You may already know where you want the film to be shot, or perhaps you have specific locations and sets you wish to use. Once you have identified your locations and scenes it's time to begin figuring out what elements you will need for each one. One example is if you are unsure of the exact model you want but decide that you require a car. This is where you can look up car models online and narrow down your options by choosing from different makes and models.
Once you have found the right car, you can start thinking about extras. Do you need people sitting in the front seats? Maybe you need someone to move around in the back. Maybe you'd like to change the interior from black to a white color. These questions will help to determine the style and feel of your car. Also, think about what kind of shots you would like to capture. What type of shots will you choose? Maybe you want to show the engine and the steering wheel. All of these things will help you identify the exact style of car you want to film.
Once you have determined all of the above, you can move on to creating a schedule. You will know when you should start and when you should finish shooting. Every day will have a time for you to arrive at the location, leave when you are leaving and return home when you are done. Everyone knows exactly what they should do and when. Hire extra staff by booking them ahead of time. It is not worth hiring someone who won’t show up because you didn’t tell him.
Your schedule will also have to be adjusted to reflect the number of days required to film. Some projects are quick and easy, while others take weeks. When you are creating your schedule, you should always keep in mind whether you need more than one shot per day or not. Multiplying takes in the same area will result both in increased costs and a longer time. If you aren't sure whether you need multiple shots, it is best to take fewer photos than you would like.
Budgeting is another important aspect of production planning. You will be able to manage your resources if you have a realistic budget. Keep in mind that you can always reduce your budget if you face unexpected difficulties. You shouldn't underestimate the amount you'll spend. You'll end up with less money after paying for other things if the cost is underestimated.
Production planning can be a complex process. However, once you know how everything works together it will become easier to plan future projects.
What are the 7 Rs of logistics.
The 7R's of Logistics is an acronym for the seven basic principles of logistics management. It was created by the International Association of Business Logisticians and published in 2004 under its "Seven Principles of Logistics Management".
The acronym is made up of the following letters:
-
Responsible – ensure that all actions are legal and don't cause harm to anyone else.
-
Reliable – have faith in your ability and capability to keep promises.
-
Use resources effectively and sparingly.
-
Realistic - Consider all aspects of operations, including environmental impact and cost effectiveness.
-
Respectful: Treat others with fairness and equity
-
Reliable - Find ways to save money and increase your productivity.
-
Recognizable - Provide value-added services to customers
How is a production manager different from a producer planner?
The major difference between a Production Planner and a Project Manager is that a Project Manager is often the person responsible for organizing and planning the entire project. While a Production Planner is involved mainly in the planning stage,
What is the importance of automation in manufacturing?
Not only are service providers and manufacturers important, but so is automation. It allows them to offer services faster and more efficiently. It reduces human errors and improves productivity, which in turn helps them lower their costs.
What are the essential elements of running a logistics firm?
To run a successful logistics company, you need a lot knowledge and skills. To communicate effectively with clients and suppliers, you must be able to communicate well. You will need to know how to interpret data and draw conclusions. You must be able to work well under pressure and handle stressful situations. To increase efficiency and creativity, you need to be creative. Strong leadership qualities are essential to motivate your team and help them achieve their organizational goals.
To meet tight deadlines, you must also be efficient and organized.
Statistics
- According to a Statista study, U.S. businesses spent $1.63 trillion on logistics in 2019, moving goods from origin to end user through various supply chain network segments. (netsuite.com)
- In 2021, an estimated 12.1 million Americans work in the manufacturing sector.6 (investopedia.com)
- Many factories witnessed a 30% increase in output due to the shift to electric motors. (en.wikipedia.org)
- (2:04) MTO is a production technique wherein products are customized according to customer specifications, and production only starts after an order is received. (oracle.com)
- It's estimated that 10.8% of the U.S. GDP in 2020 was contributed to manufacturing. (investopedia.com)
External Links
How To
How to use 5S to increase Productivity in Manufacturing
5S stands for "Sort", 'Set In Order", 'Standardize', & Separate>. Toyota Motor Corporation created the 5S methodology in 1954. It improves the work environment and helps companies to achieve greater efficiency.
The basic idea behind this method is to standardize production processes, so they become repeatable, measurable, and predictable. Cleaning, sorting and packing are all done daily. This knowledge allows workers to be more efficient in their work because they are aware of what to expect.
Implementing 5S requires five steps. These are Sort, Set In Order, Standardize. Separate. And Store. Each step involves a different action which leads to increased efficiency. By sorting, for example, you make it easy to find the items later. When you set items in an order, you put items together. Then, after you separate your inventory into groups, you store those groups in containers that are easy to access. Labeling your containers will ensure that everything is correctly labeled.
Employees will need to be more critical about their work. Employees must understand why they do certain tasks and decide if there's another way to accomplish them without relying on the old ways of doing things. In order to use the 5S system effectively, they must be able to learn new skills.
In addition to improving efficiency, the 5S system also increases morale and teamwork among employees. Once they start to notice improvements, they are motivated to keep working towards their goal of increasing efficiency.