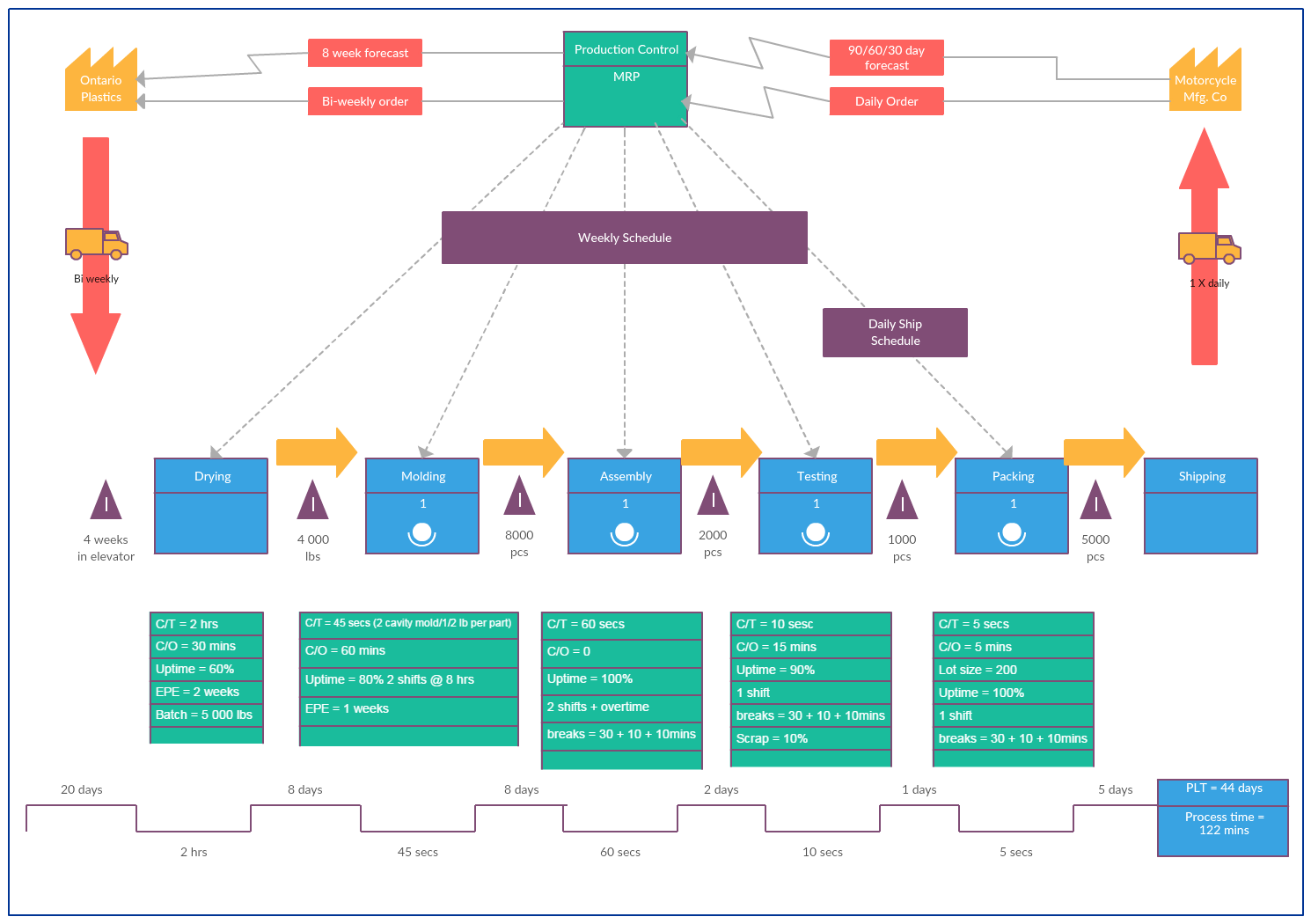
Continuous improvement is built on the principles of PDCA (Plan, Do, Check, Act). This method of improvement is highly effective, and can produce significant results if it is implemented correctly. Employee involvement is crucial to continuous improvement. A variety of resources are needed to implement the process. Measurement and Costs are important to the process, but are not its only benefit. Without employees and customers, the PDCA cycle will not be complete.
PDCA cycle
Continuous improvement means that you must apply the PDCA process to every aspect your business. The cycle involves continuously improving processes and building upon previous successes. The team may find new patterns in data, or they may discover a baseline. Both of these can reveal areas that need improvement. The PDCA Cycle is a great tool for identifying improvements opportunities. However, you must use it carefully and in a controlled way.
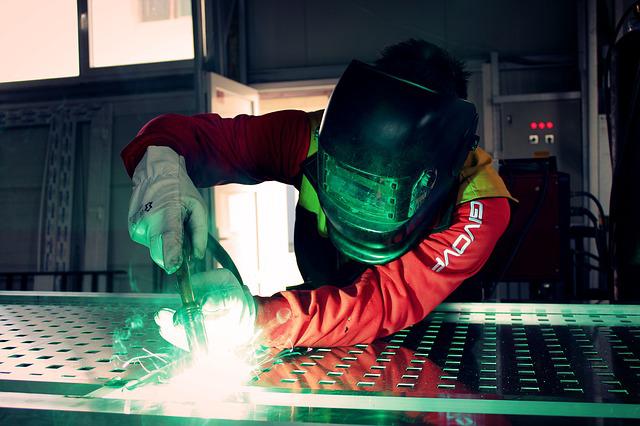
Employee participation
Although employee involvement is often called many things, it is a concept that all organizations recognize as important. Research has shown that employee engagement is directly linked to positive work outcomes. Employee involvement can be categorized into several types: representative participation through unions, direct communication, upward problem solving, and teamwork. These types are often reinforced by an organization's culture, environment, or leadership. These are some examples for employee involvement.
Measuring
Many companies now incorporate measurements into their continuous improvement programs. W. Edwards Deming introduced The Deming Cycle. This cycle includes a Check phase which assesses how well an improvement program is meeting its goals. If results are less than expected, modifications are made to the process. The cycle is repeated unless the results are satisfactory. These are part of continuous improvement.
Costs
For CI to be considered cost-effective, it is essential that an enterprise-wide cost evaluation of CI efforts be done. Cost-benefit analyses should be driven by the business imperative of increasing customer satisfaction and employee involvement scores. To ensure success, the cost-benefit analysis must also consider the ROI of CI initiatives as well as the fine-tuning budgets. The cost-benefit analysis should focus on improving the performance of key business processes and key performance areas by benchmarking them with leading competitors and industry averages.
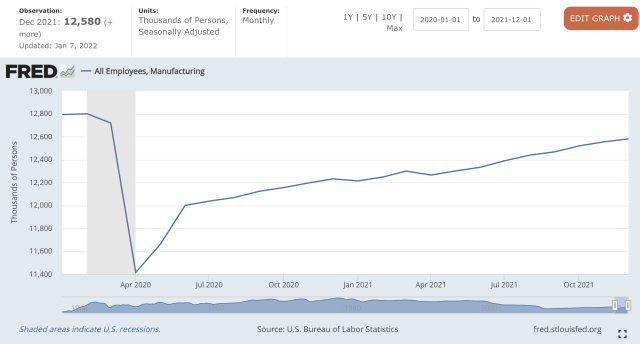
Benefits
Continuous improvement brings clear benefits. A process that focuses on learning and failure is more likely to lead to major breakthroughs. If you encourage your employees to identify potential areas of improvement, it will help them take control of their work and make the company feel invested in them. A team that invests in the testing of new technologies or tools can also result in empowered employees. You will also save money by focusing on continuous improvement. Employee satisfaction is improved and work can be made easier by making positive changes.
FAQ
What is the role of a manager in manufacturing?
The manufacturing manager should ensure that every manufacturing process is efficient and effective. They must also be alert to any potential problems and take appropriate action.
They must also be able to communicate with sales and marketing departments.
They should be up to date on the latest trends and be able apply this knowledge to increase productivity and efficiency.
How can we increase manufacturing efficiency?
First, identify the factors that affect production time. We then need to figure out how to improve these variables. If you don’t know how to start, look at which factors have the greatest impact upon production time. Once you've identified them, try to find solutions for each of those factors.
What are the four types in manufacturing?
Manufacturing is the process by which raw materials are transformed into useful products through machines and processes. It involves many different activities such as designing, building, testing, packaging, shipping, selling, servicing, etc.
How can manufacturing avoid production bottlenecks
Avoiding production bottlenecks is as simple as keeping all processes running smoothly, from the time an order is received until the product ships.
This includes planning to meet capacity requirements and quality control.
Continuous improvement techniques such Six Sigma can help you achieve this.
Six Sigma can be used to improve the quality and decrease waste in all areas of your company.
It focuses on eliminating variation and creating consistency in your work.
What type of jobs is there in logistics
There are many kinds of jobs available within logistics. These are some of the jobs available in logistics:
-
Warehouse workers - They load and unload trucks and pallets.
-
Transport drivers - These are people who drive trucks and trailers to transport goods or perform pick-ups.
-
Freight handlers – They sort and package freight at warehouses.
-
Inventory managers: They are responsible for the inventory and management of warehouses.
-
Sales representatives: They sell products to customers.
-
Logistics coordinators: They plan and manage logistics operations.
-
Purchasing agents - They buy goods and services that are necessary for company operations.
-
Customer service representatives are available to answer customer calls and emails.
-
Ship clerks - They issue bills and process shipping orders.
-
Order fillers are people who fill orders based only on what was ordered.
-
Quality control inspectors – They inspect incoming and outgoing products to ensure that there are no defects.
-
Others - There is a variety of other jobs in logistics. These include transportation supervisors and cargo specialists.
Statistics
- You can multiply the result by 100 to get the total percent of monthly overhead. (investopedia.com)
- According to a Statista study, U.S. businesses spent $1.63 trillion on logistics in 2019, moving goods from origin to end user through various supply chain network segments. (netsuite.com)
- In the United States, for example, manufacturing makes up 15% of the economic output. (twi-global.com)
- Job #1 is delivering the ordered product according to specifications: color, size, brand, and quantity. (netsuite.com)
- (2:04) MTO is a production technique wherein products are customized according to customer specifications, and production only starts after an order is received. (oracle.com)
External Links
How To
How to Use Lean Manufacturing for the Production of Goods
Lean manufacturing refers to a method of managing that seeks to improve efficiency and decrease waste. It was developed in Japan during the 1970s and 1980s by Taiichi Ohno, who received the Toyota Production System (TPS) award from TPS founder Kanji Toyoda. Michael L. Watkins published the original book on lean manufacturing, "The Machine That Changed the World," in 1990.
Lean manufacturing refers to a set of principles that improve the quality, speed and costs of products and services. It emphasizes eliminating waste and defects throughout the value stream. Lean manufacturing is also known as just in time (JIT), zero defect total productive maintenance(TPM), and five-star (S). Lean manufacturing emphasizes reducing non-value-added activities like inspection, rework and waiting.
In addition to improving product quality and reducing costs, lean manufacturing helps companies achieve their goals faster and reduces employee turnover. Lean manufacturing can be used to manage all aspects of the value chain. Customers, suppliers, distributors, retailers and employees are all included. Lean manufacturing practices are widespread in many industries. Toyota's philosophy, for example, is what has enabled it to be successful in electronics, automobiles, medical devices, healthcare and chemical engineering as well as paper and food.
Five fundamental principles underlie lean manufacturing.
-
Define Value - Identify the value your business adds to society and what makes you different from competitors.
-
Reduce waste - Stop any activity that isn't adding value to the supply chains.
-
Create Flow - Make sure work runs smoothly without interruptions.
-
Standardize and Simplify – Make processes as consistent, repeatable, and as simple as possible.
-
Build Relationships - Establish personal relationships with both internal and external stakeholders.
Lean manufacturing isn’t new, but it has seen a renewed interest since 2008 due to the global financial crisis. Many businesses have adopted lean production techniques to make them more competitive. According to some economists, lean manufacturing could be a significant factor in the economic recovery.
Lean manufacturing, which has many benefits, is now a standard practice in the automotive industry. These include improved customer satisfaction, reduced inventory levels, lower operating costs, increased productivity, and better overall safety.
It can be applied to any aspect of an organisation. It is especially useful for the production aspect of an organization, as it ensures that every step in the value chain is efficient and effective.
There are three types of lean manufacturing.
-
Just-in Time Manufacturing: This lean manufacturing method is commonly called "pull systems." JIT stands for a system where components are assembled on the spot rather than being made in advance. This method reduces lead times, increases availability, and decreases inventory.
-
Zero Defects Manufacturing - ZDM: ZDM focuses its efforts on making sure that no defective units leave a manufacturing facility. You should repair any part that needs to be repaired during an assembly line. This applies to finished goods that may require minor repairs before shipment.
-
Continuous Improvement (CI),: Continuous improvement aims improve the efficiency and effectiveness of operations by continuously identifying issues and making changes to reduce waste. Continuous improvement refers to continuous improvement of processes as well people and tools.