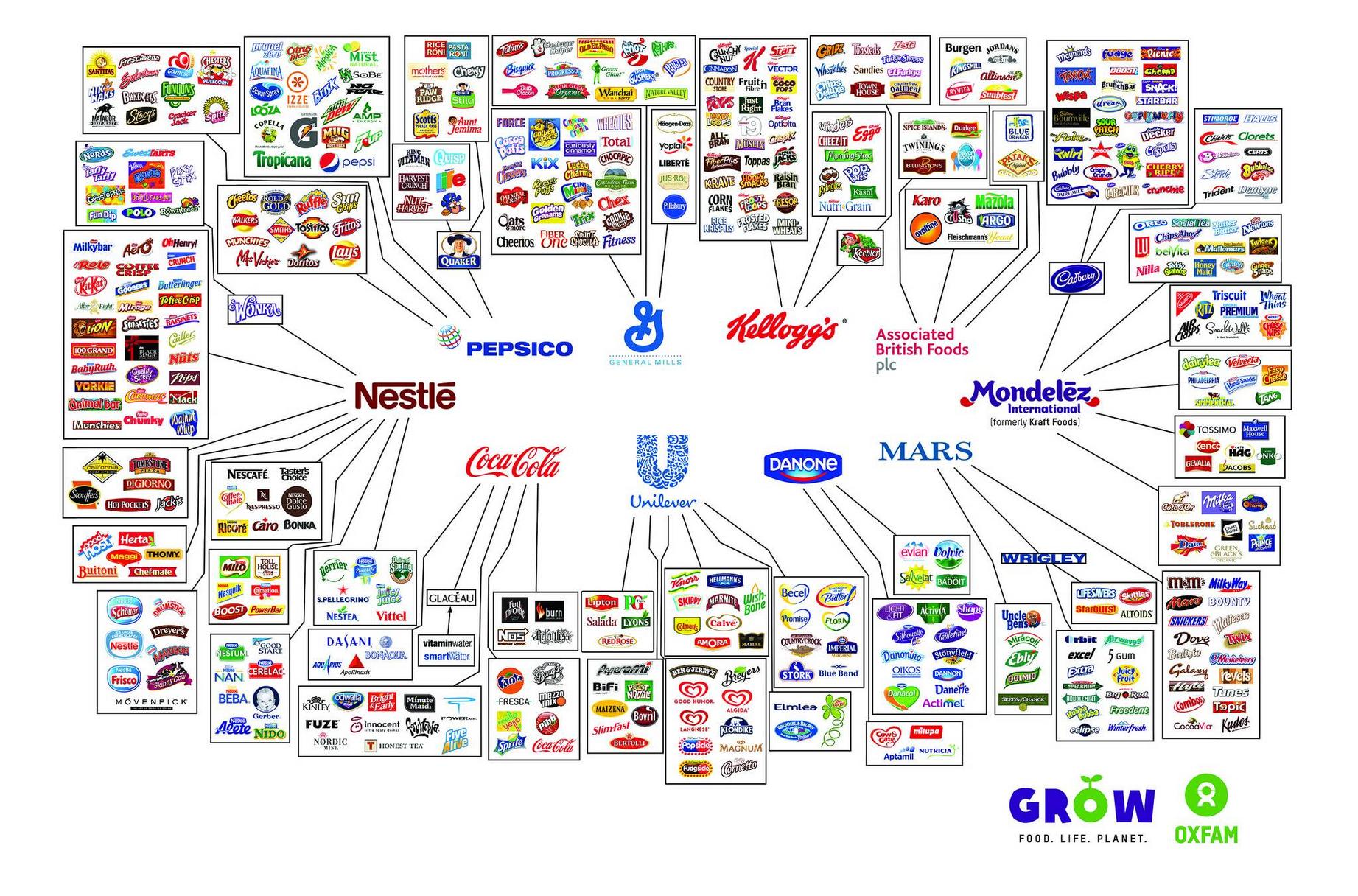
Manufacturing Phoenix, an Arizona company, provides a variety of products to the federal governments. It also provides similar products for commercial and individual clients. The dedicated facility allows production to be done under one roof with all resources within walking distance. Since its inception, the company offers opportunities for persons with disabilities. It employs approximately 70 people in its manufacturing segment.
Honeywell Aerospace
Honeywell Aerospace in Phoenix is an aerospace company that designs innovative transportation solutions. The company's products improve flight safety and fuel efficiency as well as improving runway traffic. The products of Honeywell Aerospace are used in almost every commercial airliner. Honeywell Aerospace also developed technology that was crucial in the creation of 2001: A Space Odyssey. Honeywell Aerospace also produces systems for the International Space Station.
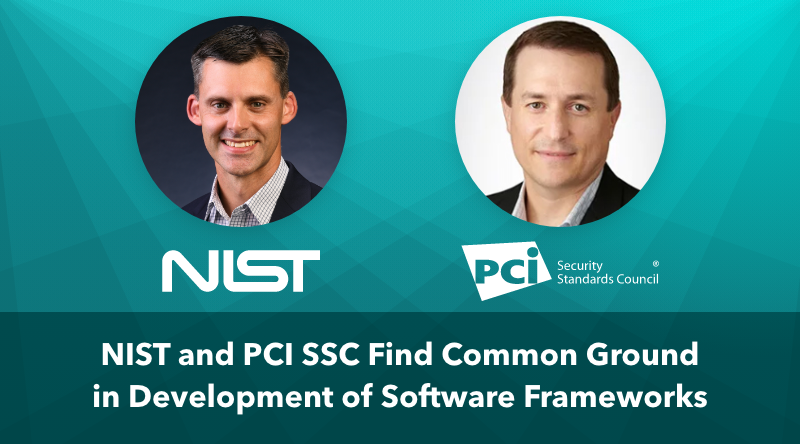
Honeywell established a Phoenix-based reactive metal alloy additive manufacturing plant in 2016. The facility converted an existing flame spray facility into a production line for parts made from titanium and aluminum alloys. Honeywell intends to start producing Inconel 718 parts in this facility by 2017. The facility is home to more than $25 million of investment by Honeywell.
Raytheon Technologies Corp.
Raytheon Technologies Corp. is an international aerospace and defense conglomerate headquartered in Arlington, Virginia. The company is the world's largest manufacturer of military equipment. The company's products include missiles, rockets and aircraft. Raytheon, a leader in aerospace and defense manufacturing, also develops advanced technologies to be commercially used.
Raytheon has a long tradition in aerospace and defense. For example, the company's aerial navigation system division accounts for 27.4%. It also manufactures electrical and mechanical equipment for planes.
Benchmark Electronics
Benchmark Electronics is an Arizona-based contract electronics manufacturing company. With more than 13,000 employees around the globe, the Phoenix-based ODM ranks among the top in the world. The company has offices at Tempe Marketplace, Scottsdale, and Tempe Marketplace. Gayla Delly was recently promoted to CEO.
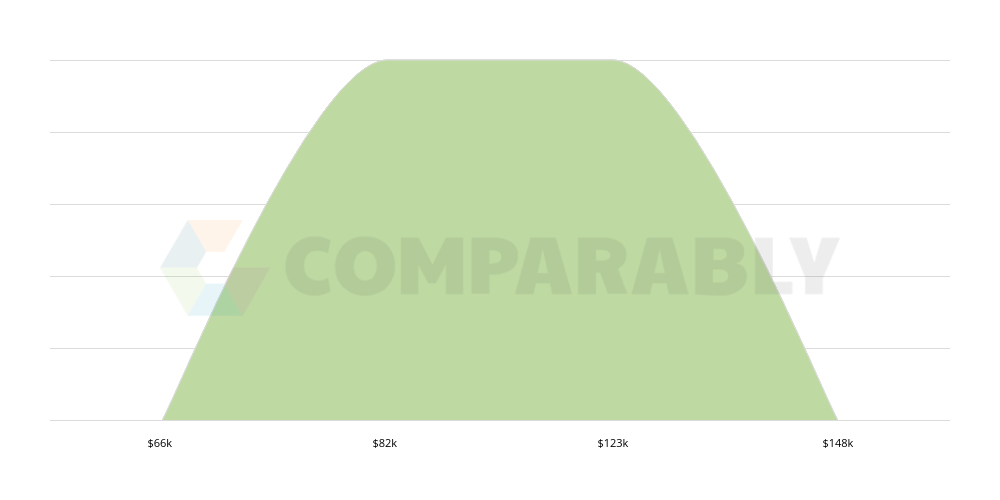
The Phoenix manufacturing facility provides vertically integrated engineering services and manufacturing. Its capabilities include microwave and RF components, embedded electronics design, and high-frequency circuits. The company also offers aftermarket solutions. It serves a wide variety of customers within the defense, industrial and commercial aerospace markets.
FAQ
What is production management?
Production planning is the process of creating a plan that covers all aspects of production. This includes scheduling, budgeting and crew, location, equipment, props, and more. This document aims to ensure that everything is planned and ready when you are ready to shoot. It should also contain information on achieving the best results on set. This information includes locations, crew details and equipment requirements.
The first step is to decide what you want. You may already know where you want the film to be shot, or perhaps you have specific locations and sets you wish to use. Once you have identified your locations and scenes it's time to begin figuring out what elements you will need for each one. For example, you might decide that you need a car but don't know exactly what model you want. You could look online for cars to see what options are available, and then narrow down your choices by selecting between different makes or models.
Once you have found the right car, you can start thinking about extras. Do you need people sitting in the front seats? Or maybe you just need someone to push the car around. You may want to change the interior's color from black or white. These questions will help determine the look and feel you want for your car. Another thing you can do is think about what type of shots are desired. What type of shots will you choose? Maybe you want to show the engine and the steering wheel. These factors will help you determine which car style you want to film.
Once you have determined all of the above, you can move on to creating a schedule. You can use a schedule to determine when and where you need it to be shot. The schedule will show you when to get there, what time to leave, and when to return home. Everyone knows exactly what they should do and when. Hire extra staff by booking them ahead of time. It is not worth hiring someone who won’t show up because you didn’t tell him.
It is important to calculate the amount of filming days when you are creating your schedule. Some projects may only take a couple of days, while others could last for weeks. You should consider whether you will need more than one shot per week when creating your schedule. Multiple takes of the same location will lead to higher costs and take more time. If you aren't sure whether you need multiple shots, it is best to take fewer photos than you would like.
Budget setting is an important part of production planning. As it will allow you and your team to work within your financial means, setting a realistic budget is crucial. Keep in mind that you can always reduce your budget if you face unexpected difficulties. You shouldn't underestimate the amount you'll spend. If you underestimate the cost of something, you will have less money left after paying for other items.
Planning production is a tedious process. Once you have a good understanding of how everything works together, planning future projects becomes easy.
What is the difference between manufacturing and logistics
Manufacturing is the production of goods using raw materials. Logistics manages all aspects of the supply chain, including procurement, production planning and distribution, inventory control, transportation, customer service, and transport. As a broad term, manufacturing and logistics often refer to both the creation and delivery of products.
How can manufacturing prevent production bottlenecks?
Avoiding production bottlenecks is as simple as keeping all processes running smoothly, from the time an order is received until the product ships.
This includes planning for capacity requirements as well as quality control measures.
Continuous improvement techniques such Six Sigma can help you achieve this.
Six Sigma management is a system that improves quality and reduces waste within your organization.
It is focused on creating consistency and eliminating variation in your work.
What are the 7 Rs of logistics?
The acronym 7R's of Logistic is an acronym that stands for seven fundamental principles of logistics management. It was developed and published by the International Association of Business Logisticians in 2004 as part of the "Seven Principles of Logistics Management".
The acronym is composed of the following letters.
-
Responsible – ensure that all actions are legal and don't cause harm to anyone else.
-
Reliable: Have faith in your ability or the ability to honor any promises made.
-
Be responsible - Use resources efficiently and avoid wasting them.
-
Realistic - Take into consideration all aspects of operations including cost-effectiveness, environmental impact, and other factors.
-
Respectful: Treat others with fairness and equity
-
Be resourceful: Look for opportunities to save money or increase productivity.
-
Recognizable: Provide customers with value-added service
What are the four types of manufacturing?
Manufacturing is the process that transforms raw materials into useful products. It can involve many activities like designing, manufacturing, testing packaging, shipping, selling and servicing.
How can manufacturing efficiency be improved?
The first step is to identify the most important factors affecting production time. Then we need to find ways to improve these factors. If you don’t know where to begin, consider which factors have the largest impact on production times. Once you identify them, look for solutions.
Statistics
- (2:04) MTO is a production technique wherein products are customized according to customer specifications, and production only starts after an order is received. (oracle.com)
- According to the United Nations Industrial Development Organization (UNIDO), China is the top manufacturer worldwide by 2019 output, producing 28.7% of the total global manufacturing output, followed by the United States, Japan, Germany, and India.[52][53] (en.wikipedia.org)
- According to a Statista study, U.S. businesses spent $1.63 trillion on logistics in 2019, moving goods from origin to end user through various supply chain network segments. (netsuite.com)
- In the United States, for example, manufacturing makes up 15% of the economic output. (twi-global.com)
- [54][55] These are the top 50 countries by the total value of manufacturing output in US dollars for its noted year according to World Bank.[56] (en.wikipedia.org)
External Links
How To
How to Use 5S to Increase Productivity in Manufacturing
5S stands for "Sort", 'Set In Order", 'Standardize', & Separate>. The 5S methodology was developed at Toyota Motor Corporation in 1954. It improves the work environment and helps companies to achieve greater efficiency.
This method has the basic goal of standardizing production processes to make them repeatable. Cleaning, sorting and packing are all done daily. Through these actions, workers can perform their jobs more efficiently because they know what to expect from them.
There are five steps that you need to follow in order to implement 5S. Each step has a different action and leads to higher efficiency. If you sort items, it makes them easier to find later. When you set items in an order, you put items together. Once you have separated your inventory into groups and organized them, you will store these groups in easily accessible containers. Make sure everything is correctly labeled when you label your containers.
This requires employees to critically evaluate how they work. Employees should understand why they do the tasks they do, and then decide if there are better ways to accomplish them. In order to use the 5S system effectively, they must be able to learn new skills.
In addition to improving efficiency, the 5S system also increases morale and teamwork among employees. As they begin to see improvements, they feel motivated to continue working towards the goal of achieving higher levels of efficiency.