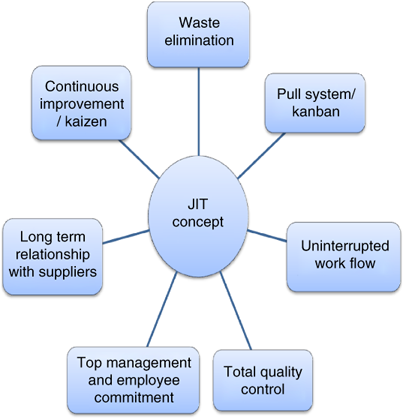
Six-Sigma and Lean both offer complementary methods for improving processes. Although they both have the same tools for problem solving, each has its strengths and weaknesses. Six-Sigma is a statistical process control technique, and Lean starts with the premise that a product must add value, not just produce it. Lean means reducing waste and increasing the quality of the product being made.
Problem solving with PDCA
While there are some differences between DMAIC solution solving and PDCA problem solving, they are both based on DMAIC. The PDCA cycle needs more planning and analysis. PDCA isn't as efficient for solving urgent issues like DMAIC. This approach requires a lead problem-solver with technical skills. Six Sigma practitioners are "green belts" certified.
Six Sigma is based on a cycle created by W. Edwards Deming, which was introduced in 1950. It was created to be used in combination with continuous improvement methods to rebuild Japan's industrial sectors. Real data must be collected and a clear mission statement must created in the P (Plan). After the PDCA stage, the team must decide on a recommended solution.
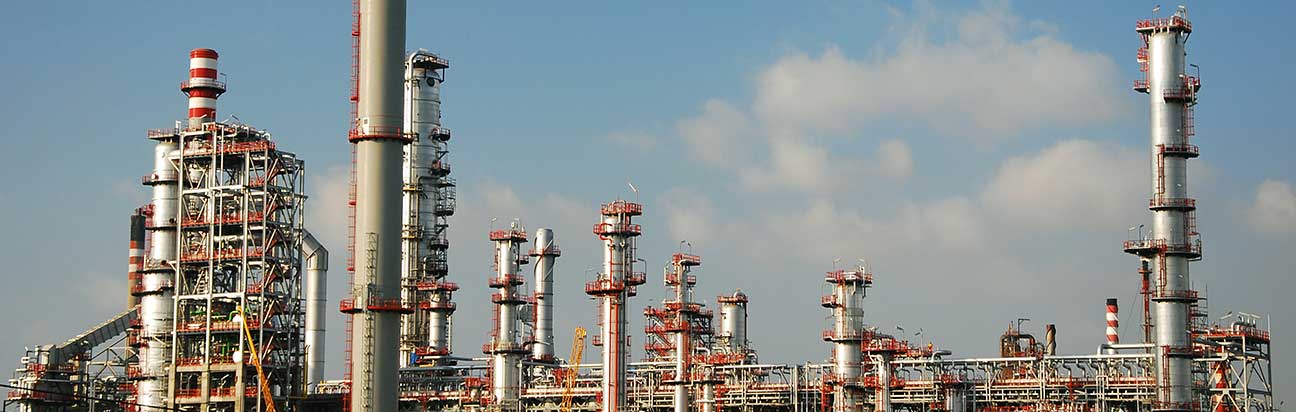
Process maps
One key difference between Six Sigma processes maps and Lean is the way each describes them. Both focus on the details of a process, but each methodology will be more focused on certain aspects. Lean, for instance, involves mapping actual processes as opposed to standard operating procedures. When creating process diagrams, you should consider the major decisions, activities, and sources for approval. Include areas that require multiple methods and factors. Check the process flow and match roles.
A process map should have steps, symbols and arrows that show the flow of a particular process. To ensure accuracy, each process should be reviewed and approved by multiple people. The date the process map was created should be included, along with contact information for anyone who has questions. Overall, process maps can improve a process. However, they may be overly complex.
Analysis of cause & effect
Six Sigma and lean project managing techniques use statistical analysis and stochastic optimising. The Cause and Effect Matrix relates each step in a process to its outputs and inputs. The customer requirements are listed by importance and then inputs and outputs are ranked according their effect on the outcome. You should identify the key input variables to your process and rank them accordingly.
Although each technique is unique, they all offer different benefits. Lean Six Sigma uses a process management methodology that is based around Frederick Winslow Taylor’s Principles of Scientific Management. Taylor envisioned business processes as interlocking processes and workflows. Taylor recommended that we reduce waste and eliminate variation. Six-Sigma, lean and lean can be used in conjunction to reduce waste.
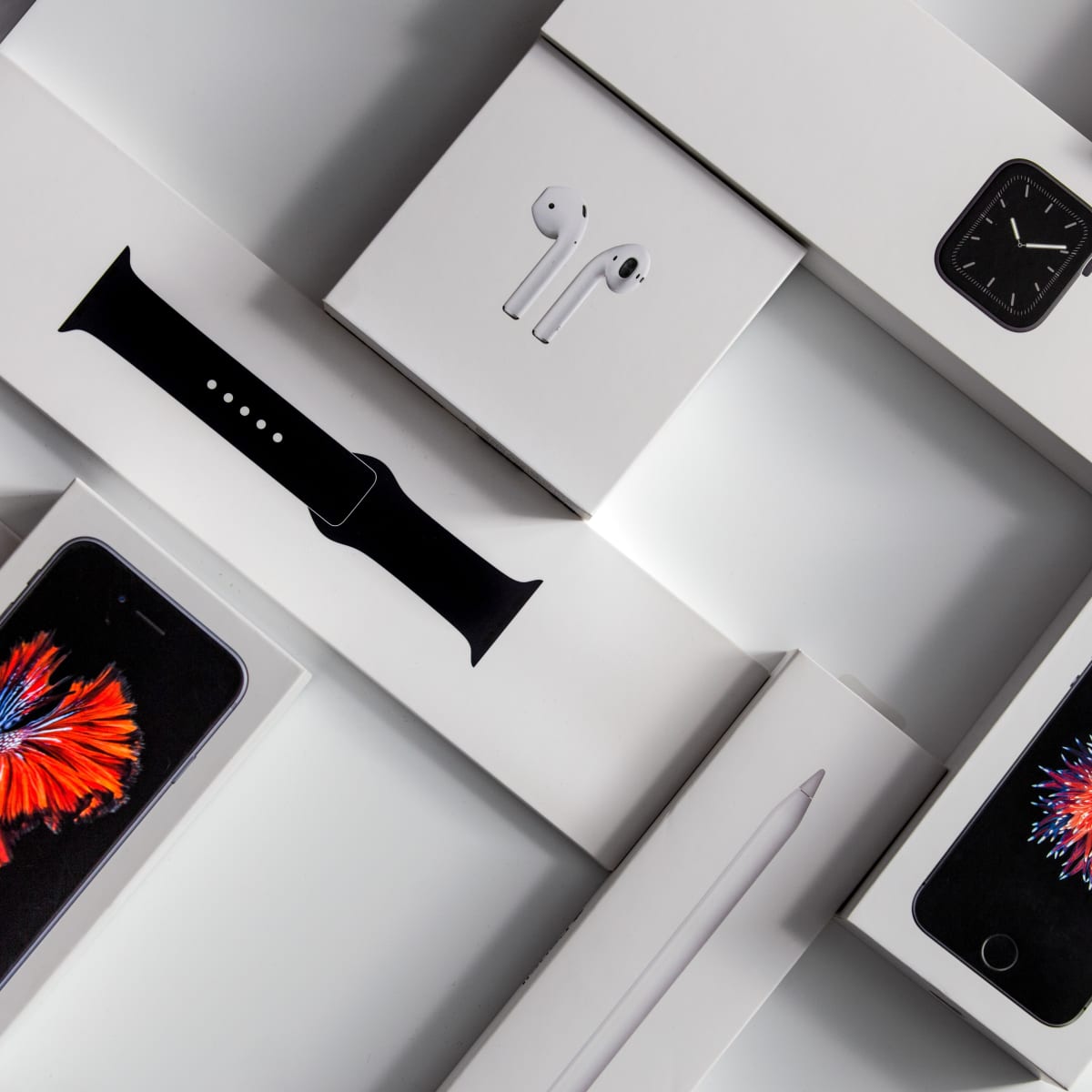
Elimination of variation
Variation is a part of any manufacturing process. This variability can create uncertainty in the result. To provide professional results, consistency is necessary. Six Sigma and Lean manufacturing methods aim to eliminate variation. Some amount of variation is fine, but too much leads to repairs, rework, and possibly even out-of-business consequences. It is best to identify the root causes of variation.
The decision points are the best place to search for variations. Process maps show decision points and are represented by diamonds. Six Sigma teams can begin by identifying decision points, and then start eliminating variations. This information is obtained directly from the Six Sigma process owner. The Six Sigma Team cannot focus on any process that the owner isn't following a standardized process. If the Six Sigma team does not have sufficient technical ability to make adjustments, a process diagram may not be useful.
FAQ
What does manufacturing mean?
Manufacturing Industries are those businesses that make products for sale. These products are sold to consumers. This is accomplished by using a variety of processes, including production, distribution and retailing. They make goods from raw materials with machines and other equipment. This includes all types if manufactured goods.
Do we need to know about Manufacturing Processes before learning about Logistics?
No. It doesn't matter if you don't know anything about manufacturing before you learn about logistics. Knowing about manufacturing processes will help you understand how logistics works.
What is the difference between manufacturing and logistics
Manufacturing is the process of creating goods from raw materials by using machines and processes. Logistics includes all aspects related to supply chain management, such as procurement, distribution planning, inventory control and transportation. Manufacturing and logistics can often be grouped together to describe a larger term that covers both the creation of products, and the delivery of them to customers.
Why automate your warehouse
Modern warehouses are increasingly dependent on automation. E-commerce has increased the demand for quicker delivery times and more efficient processes.
Warehouses should be able adapt quickly to new needs. Technology is essential for warehouses to be able to adapt quickly to changing needs. Automating warehouses is a great way to save money. These are just a few reasons to invest in automation.
-
Increases throughput/productivity
-
Reduces errors
-
Accuracy is improved
-
Safety increases
-
Eliminates bottlenecks
-
This allows companies to scale easily
-
This makes workers more productive
-
It gives visibility to everything that happens inside the warehouse
-
Enhances customer experience
-
Improves employee satisfaction
-
It reduces downtime, and increases uptime
-
Ensures quality products are delivered on time
-
Human error can be eliminated
-
Assure compliance with regulations
What are the 7 Rs of logistics?
The 7R's of Logistics is an acronym for the seven basic principles of logistics management. It was published in 2004 by the International Association of Business Logisticians as part of their "Seven Principles of Logistics Management" series.
The acronym is composed of the following letters.
-
Responsible - ensure that actions are in compliance with legal requirements and do not cause harm to others.
-
Reliable - have confidence in the ability to deliver on commitments made.
-
Reasonable - use resources efficiently and don't waste them.
-
Realistic – Consider all aspects, including cost-effectiveness as well as environmental impact.
-
Respectful - treat people fairly and equitably.
-
Reliable - Find ways to save money and increase your productivity.
-
Recognizable is a company that provides customers with value-added solutions.
How can I learn about manufacturing?
The best way to learn about manufacturing is through hands-on experience. You can read books, or watch instructional videos if you don't have the opportunity to do so.
Statistics
- Many factories witnessed a 30% increase in output due to the shift to electric motors. (en.wikipedia.org)
- Job #1 is delivering the ordered product according to specifications: color, size, brand, and quantity. (netsuite.com)
- According to the United Nations Industrial Development Organization (UNIDO), China is the top manufacturer worldwide by 2019 output, producing 28.7% of the total global manufacturing output, followed by the United States, Japan, Germany, and India.[52][53] (en.wikipedia.org)
- You can multiply the result by 100 to get the total percent of monthly overhead. (investopedia.com)
- In the United States, for example, manufacturing makes up 15% of the economic output. (twi-global.com)
External Links
How To
How to Use 5S to Increase Productivity in Manufacturing
5S stands in for "Sort", the "Set In Order", "Standardize", or "Separate". Toyota Motor Corporation was the first to develop the 5S approach in 1954. It helps companies achieve higher levels of efficiency by improving their work environment.
The idea behind standardizing production processes is to make them repeatable and measurable. It means tasks like cleaning, sorting or packing, labeling, and storing are done every day. This knowledge allows workers to be more efficient in their work because they are aware of what to expect.
Implementing 5S involves five steps: Sort, Set in Order, Standardize Separate, Store, and Each step requires a different action to increase efficiency. If you sort items, it makes them easier to find later. When you arrange items, you place them together. After you have divided your inventory into groups you can store them in easy-to-reach containers. Labeling your containers will ensure that everything is correctly labeled.
This requires employees to critically evaluate how they work. Employees must understand why they do certain tasks and decide if there's another way to accomplish them without relying on the old ways of doing things. To be successful in the 5S system, employees will need to acquire new skills and techniques.
The 5S method not only increases efficiency but also boosts morale and teamwork. Once they start to notice improvements, they are motivated to keep working towards their goal of increasing efficiency.