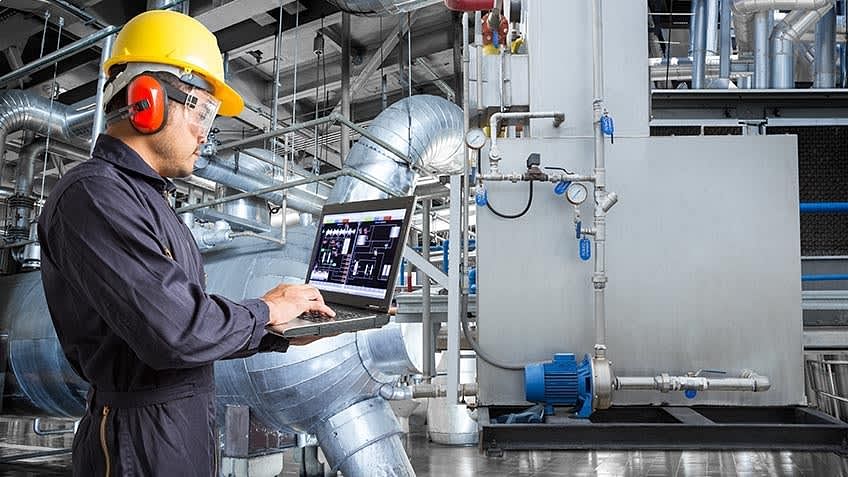
Lean can be used as an acronym in the manufacturing world to describe certain principles and techniques. It can also serve as a motivating term that encourages process improvement.
The Definition Of Lean
In order to improve efficiency, a business may have to cut out certain activities which don't add any value to its product or services. This can include idle resources, unused equipment, or other resources that have not been used to the fullest extent.
This is lean management's main goal, which is to remove waste in the production process. This process is never-ending, which means that it must always be improved and adjusted.
The lean concept is based upon the idea that companies should put their focus on what their customers want, and give it priority over what they believe they need. By doing this, businesses avoid wasting resources or time on creating products that customers aren't interested in.
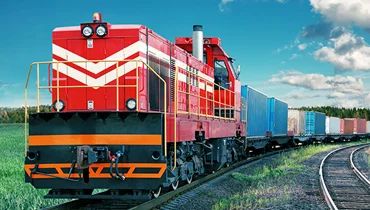
You should be aware that the lean concept can be adapted to any type of industry or production process. This is why it has become so popular in many different industries.
Lean manufacturing has been around for many years. It is a system which focuses delivering the best products in the most efficient way. It is a fantastic tool for improving the efficiency of manufacturing processes.
Toyoda Toyoda is the founder of Toyota. The concept of lean focuses on eliminating waste during production. It includes defects and other waste that would be unacceptable to the customer.
Toyoda came up with a solution that involved a flow-process, where workers would stop the production line and inspect an item. If necessary, they would remove it. The company was able to optimize each stage of production to reduce defects and increase productivity.
Jidoka, or automatic stoppage of production when an abnormality occurs in the process is what this system is. This is known as kaizen, and is a key part of the lean manufacturing process.
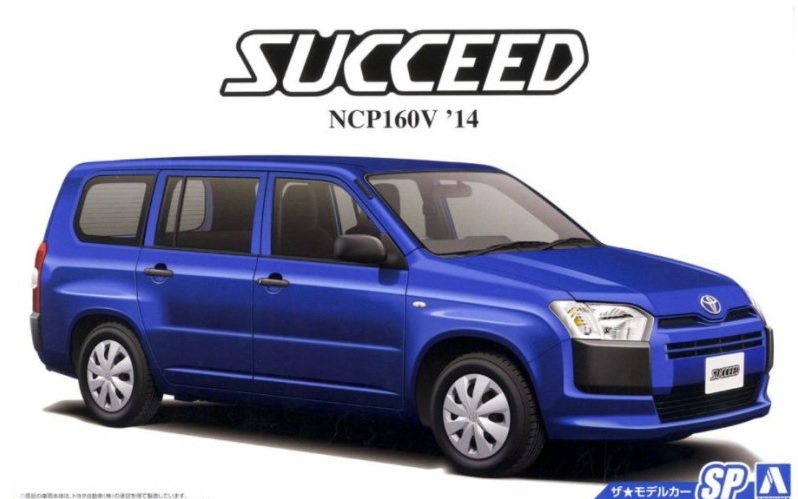
Kaizen is the process of continuous improvement in any process. This process can be applied in any area of business, whether it is the production of products.
Lean is a concept many people do not fully grasp, but which can be a very useful tool to improve business operations. Lean can save companies money and time, while also helping them to build a stronger reputation with their customers.
Lean isn't an isolated process; it is a system that must be improved on all levels within a company to achieve success. It's important to involve everyone in the process. This way, they can each contribute their own ideas and help ensure that things run smoothly.
FAQ
How does a production planner differ from a project manager?
The primary difference between a producer planner and a manager of a project is that the manager usually plans and organizes the whole project, while a production planner is only involved in the planning stage.
What are the responsibilities of a production planner
Production planners ensure all aspects of the project are delivered within time and budget. A production planner ensures that the service and product meet the client's expectations.
Why automate your warehouse
Modern warehousing is becoming more automated. E-commerce has brought increased demand for more efficient and quicker delivery times.
Warehouses have to be flexible to meet changing requirements. Technology investment is necessary to enable warehouses to respond quickly to changing demands. Automation warehouses can bring many benefits. Here are some of the reasons automation is worth your investment:
-
Increases throughput/productivity
-
Reduces errors
-
Increases accuracy
-
Safety increases
-
Eliminates bottlenecks
-
Allows companies to scale more easily
-
This makes workers more productive
-
Gives you visibility into all that is happening in your warehouse
-
Enhances customer experience
-
Improves employee satisfaction
-
It reduces downtime, and increases uptime
-
You can be sure that high-quality products will arrive on time
-
Removing human error
-
It ensures compliance with regulations
What are the four types in manufacturing?
Manufacturing refers to the transformation of raw materials into useful products by using machines and processes. It includes many different activities like designing, building and testing, packaging, shipping and selling, as well as servicing.
Statistics
- Job #1 is delivering the ordered product according to specifications: color, size, brand, and quantity. (netsuite.com)
- In 2021, an estimated 12.1 million Americans work in the manufacturing sector.6 (investopedia.com)
- Many factories witnessed a 30% increase in output due to the shift to electric motors. (en.wikipedia.org)
- It's estimated that 10.8% of the U.S. GDP in 2020 was contributed to manufacturing. (investopedia.com)
- (2:04) MTO is a production technique wherein products are customized according to customer specifications, and production only starts after an order is received. (oracle.com)
External Links
How To
How to Use the 5S to Increase Productivity In Manufacturing
5S stands for "Sort", 'Set In Order", 'Standardize', & Separate>. Toyota Motor Corporation invented the 5S strategy in 1954. It helps companies achieve higher levels of efficiency by improving their work environment.
This method aims to standardize production processes so that they are repeatable, measurable and predictable. This means that daily tasks such as cleaning and sorting, storage, packing, labeling, and packaging are possible. Through these actions, workers can perform their jobs more efficiently because they know what to expect from them.
There are five steps that you need to follow in order to implement 5S. Each step requires a different action to increase efficiency. For example, when you sort things, you make them easy to find later. When you set items in an order, you put items together. Next, organize your inventory into categories and store them in containers that are easily accessible. Finally, label all containers correctly.
Employees need to reflect on how they do their jobs. Employees must be able to see why they do what they do and find a way to achieve them without having to rely on their old methods. In order to use the 5S system effectively, they must be able to learn new skills.
The 5S method increases efficiency and morale among employees. They will feel motivated to strive for higher levels of efficiency once they start to see results.