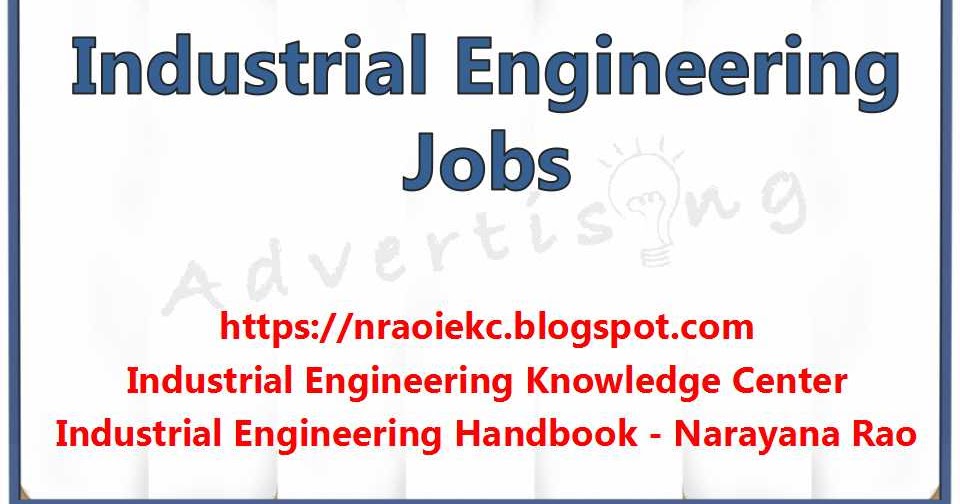
Businesses are never-ending processes, and to remain competitive they must constantly look for new ways to improve. A company can improve their operation in many ways, including productivity, operations and communication.
Operational excellence is a management technique that seeks to improve all aspects of a business's operations. This includes reducing waste, improving processes and developing efficient workflows to boost efficiency and profitability.
The term "operational excellence" is derived by Adam Smith from the 18th-century management theory of scientific leadership, which was influenced in part by Frederick Winslow Taylor, Henry Ford, and Frederick Winslow Taylor. It is a process that takes years to implement and requires a lot of trial and error, but it is worth the effort.
What is operational excellence?
The Institute for Operational Excellence defines Operational Excellence (or the ability to monitor flow of information and products within the organization) as the capability to monitor this flow. This means everyone from the senior executives to the workers on the floor should be capable of detecting issues and observing product flow.
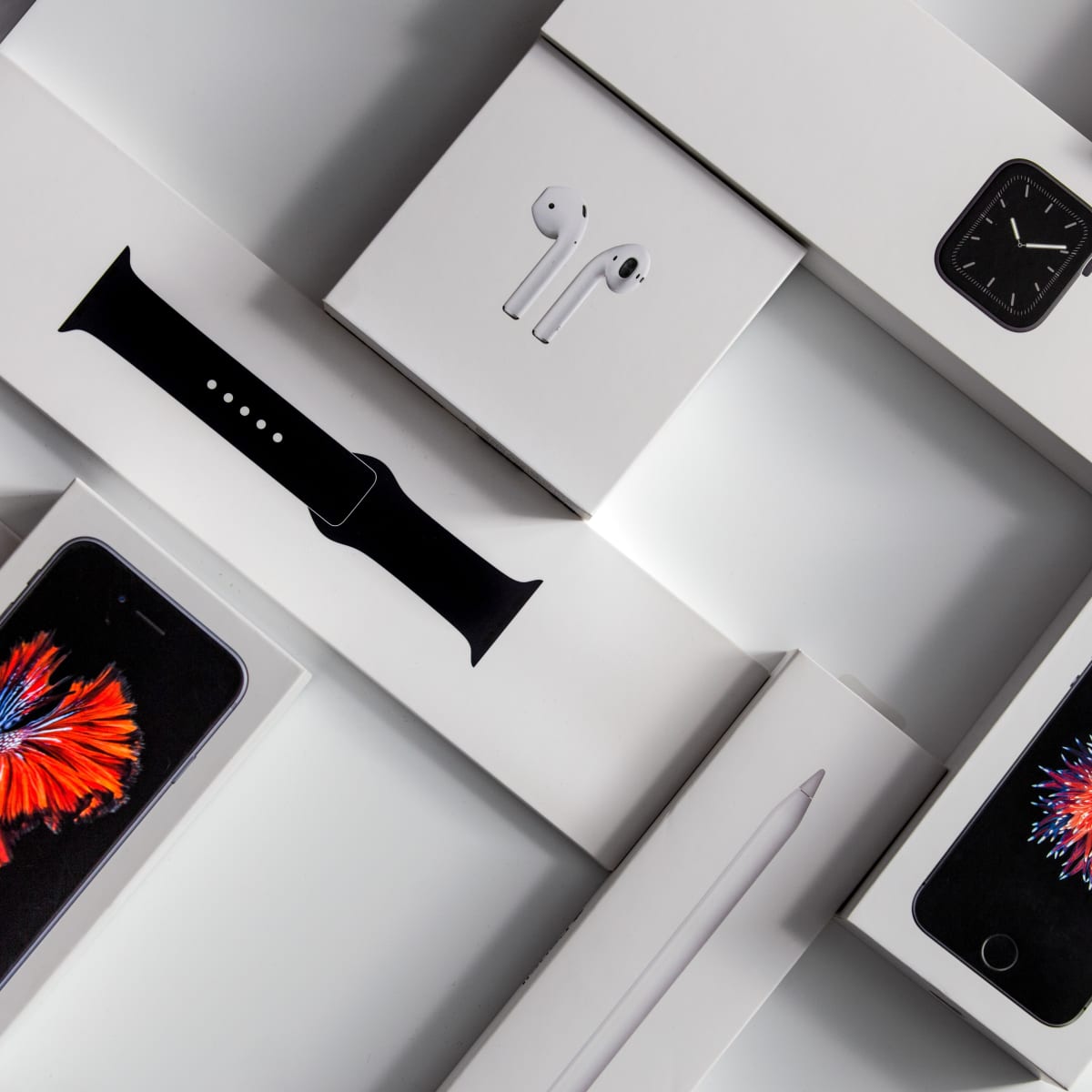
It is important to change the culture in order to achieve a culture based on excellence. This is a continuous process, and it takes some time to build employee trust. It requires a shift in leadership style and behavior.
What is Operational Excellence Staff's Role?
Operational excellence staff are responsible for implementing the strategy of the organization. Their responsibilities include managing process improvement, participating on cross-functional teams, defining and tracking performance metrics, creating a culture, and mentorship of frontline operational leaders.
They may also oversee projects that are based on methodologies of improvement, such as Six Sigma. These methods are highly effective at improving efficiency and transforming operations, but they need trained staff who have expertise in areas such as project management or business intelligence.
How to Create a Plan of Operational Excellence
A plan for operational excellence should include a methodology to help you reach your goals quickly and efficiently. This is especially true if you are looking to reduce waste, improve your workflows or enhance your customer experience.
You can also use a number of different KPIs to track your progress. These should be relevant and achievable for your employees in order to inspire them to strive to achieve excellence.
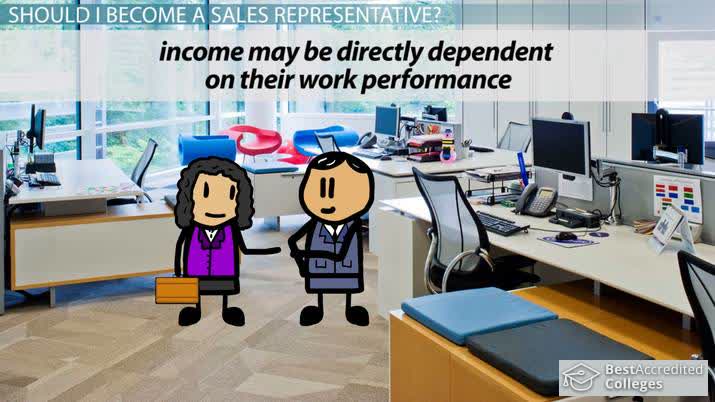
These tools can help you to ensure that your business is as cost-effective and efficient as possible. These tools allow you get feedback directly from your frontline employees so you can improve.
How to measure your operational excellence goals
Most directors of operations will use a combination of financial and operational data at a high level, along with qualitative information from employee and customer surveys. This will give them a clear picture of how they are doing and how close they are to reaching their objectives.
The reason for this is that operational excellence can be found at all levels of the organization. Therefore, it's essential to have individual targets set by each member of your team. The Director of Operations, for example, should have a target profit based on what they spend in people. The project manager, however, should have a target based around the billable and nonbillable aspects of their work. The operational excellence of an organization can then be measured on all levels. This will ensure that revenue and costs are equal.
FAQ
Is it necessary to be familiar with Manufacturing Processes before we learn about Logistics.
No. No. Knowing about manufacturing processes will help you understand how logistics works.
Can we automate some parts of manufacturing?
Yes! Since ancient times, automation has been in existence. The Egyptians created the wheel thousands years ago. Today, robots assist in the assembly of lines.
In fact, there are several applications of robotics in manufacturing today. These include:
-
Robots for assembly line
-
Robot welding
-
Robot painting
-
Robotics inspection
-
Robots that produce products
Automation can be applied to manufacturing in many other ways. 3D printing makes it possible to produce custom products in a matter of days or weeks.
How can excess manufacturing production be reduced?
The key to reducing overproduction lies in developing better ways to manage inventory. This would reduce the amount of time spent on unnecessary activities such as purchasing, storing, and maintaining excess stock. This would allow us to use our resources for more productive tasks.
You can do this by adopting a Kanban method. A Kanban board is a visual display used to track work in progress. In a Kanban system, work items move through a sequence of states until they reach their final destination. Each state is assigned a different priority.
For instance, when work moves from one stage to another, the current task is complete enough to be moved to the next stage. However, if a task is still at the beginning stages, it will remain so until it reaches the end of the process.
This helps to keep work moving forward while ensuring that no work is left behind. Managers can view the Kanban board to see how much work they have done. This data allows them adjust their workflow based upon real-time data.
Lean manufacturing is another way to manage inventory levels. Lean manufacturing focuses on eliminating waste throughout the entire production chain. Anything that doesn't add value to the product is considered waste. Here are some examples of common types.
-
Overproduction
-
Inventory
-
Packaging that is not necessary
-
Exceed materials
Manufacturers can increase efficiency and decrease costs by implementing these ideas.
Why automate your warehouse
Modern warehouses have become more dependent on automation. With the rise of ecommerce, there is a greater demand for faster delivery times as well as more efficient processes.
Warehouses must be able to quickly adapt to changing demands. In order to do this, they need to invest in technology. Automation of warehouses offers many benefits. Here are some of the reasons automation is worth your investment:
-
Increases throughput/productivity
-
Reduces errors
-
Increases accuracy
-
Safety increases
-
Eliminates bottlenecks
-
Allows companies to scale more easily
-
Workers are more productive
-
It gives visibility to everything that happens inside the warehouse
-
Enhances customer experience
-
Improves employee satisfaction
-
Reduces downtime and improves uptime
-
Quality products delivered on time
-
Eliminates human error
-
It helps ensure compliance with regulations
Statistics
- According to the United Nations Industrial Development Organization (UNIDO), China is the top manufacturer worldwide by 2019 output, producing 28.7% of the total global manufacturing output, followed by the United States, Japan, Germany, and India.[52][53] (en.wikipedia.org)
- In the United States, for example, manufacturing makes up 15% of the economic output. (twi-global.com)
- Many factories witnessed a 30% increase in output due to the shift to electric motors. (en.wikipedia.org)
- In 2021, an estimated 12.1 million Americans work in the manufacturing sector.6 (investopedia.com)
- (2:04) MTO is a production technique wherein products are customized according to customer specifications, and production only starts after an order is received. (oracle.com)
External Links
How To
How to use the Just In-Time Production Method
Just-in-time (JIT) is a method that is used to reduce costs and maximize efficiency in business processes. It is a process where you get the right amount of resources at the right moment when they are needed. This means that you only pay for what you actually use. Frederick Taylor, a 1900s foreman, first coined the term. He noticed that workers were often paid overtime when they had to work late. He then concluded that if he could ensure that workers had enough time to do their job before starting to work, this would improve productivity.
JIT is an acronym that means you need to plan ahead so you don’t waste your money. Also, you should look at the whole project from start-to-finish and make sure you have the resources necessary to address any issues. If you anticipate that there might be problems, you'll have enough people and equipment to fix them. You won't have to pay more for unnecessary items.
There are different types of JIT methods:
-
Demand-driven: This JIT is where you place regular orders for the parts/materials that are needed for your project. This will allow to track how much material has been used up. You'll also be able to estimate how long it will take to produce more.
-
Inventory-based: This allows you to store the materials necessary for your projects in advance. This allows you to predict how much you can expect to sell.
-
Project-driven: This means that you have enough money to pay for your project. Once you have an idea of how much material you will need, you can purchase the necessary materials.
-
Resource-based JIT : This is probably the most popular type of JIT. You allocate resources based on the demand. You will, for example, assign more staff to deal with large orders. If there aren't many orders, you will assign fewer people.
-
Cost-based: This is the same as resource-based except that you don't care how many people there are but how much each one of them costs.
-
Price-based: This is similar to cost-based but instead of looking at individual workers' salaries, you look at the total company price.
-
Material-based: This is quite similar to cost-based, but instead of looking at the total cost of the company, you're concerned with how much raw materials you spend on average.
-
Time-based: This is another variation of resource-based JIT. Instead of worrying about how much each worker costs, you can focus on how long the project takes.
-
Quality-based: This is yet another variation of resource-based JIT. Instead of looking at the labor costs and time it takes to make a product, think about its quality.
-
Value-based JIT: This is the latest form of JIT. This is where you don't care about how the products perform or whether they meet customers' expectations. Instead, your goal is to add value to the market.
-
Stock-based: This stock-based method focuses on the actual quantity of products being made at any given time. This method is useful when you want to increase production while decreasing inventory.
-
Just-in-time planning (JIT): This is a combination JIT and supply-chain management. It's the process of scheduling delivery of components immediately after they are ordered. It's important as it reduces leadtimes and increases throughput.