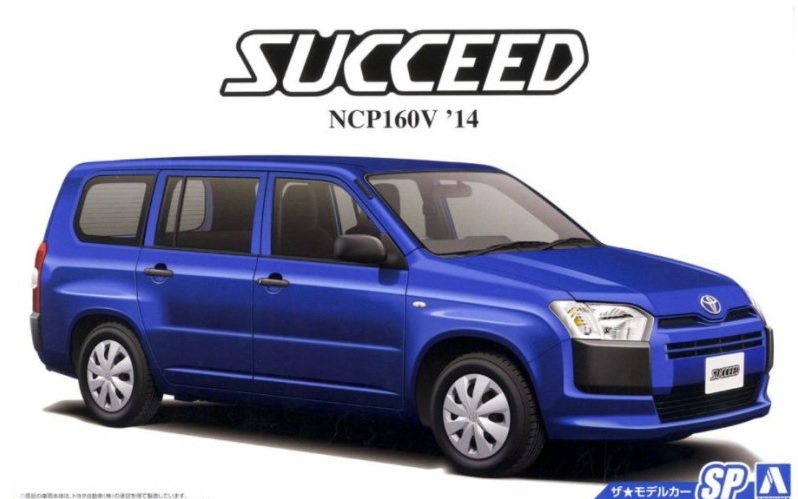
The management of a supply-chain involves many aspects. It encompasses both internal processes. Marketing also includes supply chain management. In almost all industries, supply chains are utilized. The supply chain's main purpose is to deliver goods to consumers. It is common to deliver products on schedule.
An operations manager is a person in charge of overseeing business processes. This includes supervising staffing, hiring and managing equipment. They also supervise production and planning. They will also be responsible for creating a strategy that will improve operations. The operations manager also needs to make sure that there is enough inventory for production, that it is within the company's budget, and that it meets the specifications of the company. He coordinates with the supply chain manager to ship orders to retailers and consumers.
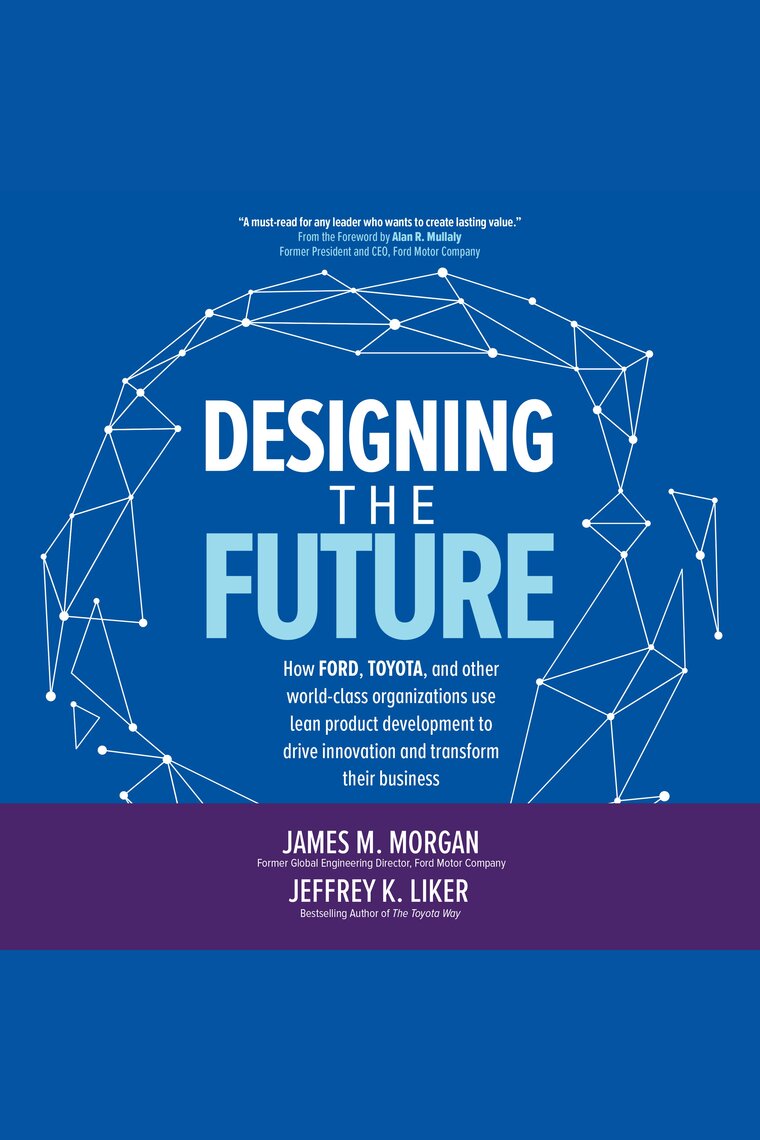
The operations and supply chains program at UTSA is designed for you to enhance your leadership and analytical skills. It is an interactive program that combines the classroom with hands-on learning. The program offers data analysis skills, business process improvement, green belt certification in Lean Six Sigma, and Lean Six Sigma. This program also covers the entire supply chain and operations. You will also have the opportunity to learn new technologies and apply them to your business.
The supply and operations program focuses on value adding processes. The program gives students the tools they need to make smarter business decisions. The program includes a number of case studies and examples from industry. It also teaches students how communicate effectively and to use computers. This program also offers minors. The minor complements the major and helps students maximize their supply chain effectiveness. The minor can also serve as a Contexts & Perspectives course and an unrestricted option.
The operations and supply chain program is a great opportunity for students to learn about how to make better business decisions. Students also have the unique opportunity to apply concepts to their own businesses. It can also be used as a stepping stone for careers in management, marketing, and technology. Students can also apply for the Lean Six Sigma greenbelt certification. It offers students the chance to meet industry professionals and learn about current technologies and trends.
Students can also learn about the process involved in creating products and services through the operations and supply chain program. This program also helps students communicate well, which is a valuable skill for both business and management.
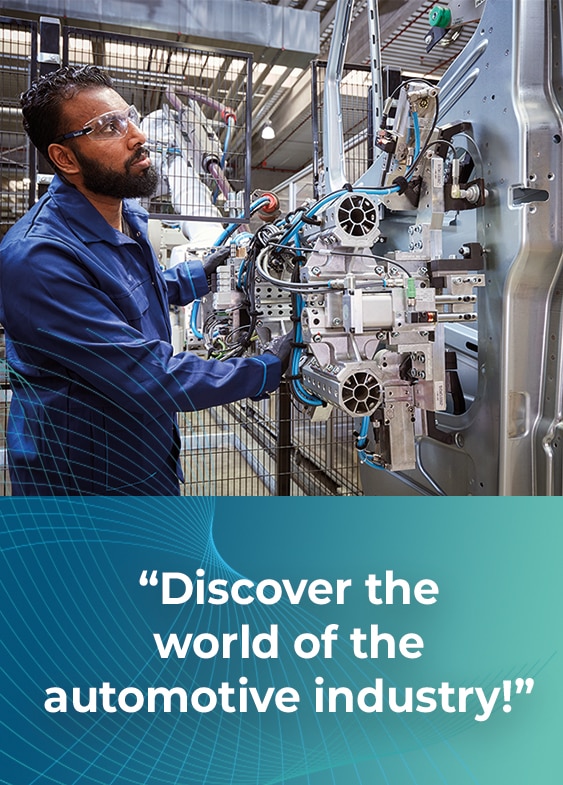
It's written in a very user-friendly way. It's appropriate for students of all backgrounds. The book not only explains how the supply chains work, but also discusses how to design supply networks. This book also offers quantitative methods of comparing supply to demand. This book also provides information on how to include customers in your supply chain.
FAQ
How can manufacturing prevent production bottlenecks?
Avoiding production bottlenecks is as simple as keeping all processes running smoothly, from the time an order is received until the product ships.
This includes both planning for capacity and quality control.
This can be done by using continuous improvement techniques, such as Six Sigma.
Six Sigma is a management system used to improve quality and reduce waste in every aspect of your organization.
It emphasizes consistency and eliminating variance in your work.
What is it like to manage a logistics company?
To be a successful businessman in logistics, you will need many skills and knowledge. You must have good communication skills to interact effectively with your clients and suppliers. You need to understand how to analyze data and draw conclusions from it. You must be able manage stress and pressure under pressure. You need to be innovative and creative to come up with new ways to increase efficiency. You need to have strong leadership qualities to motivate team members and direct them towards achieving organizational goals.
You must be organized to meet tight deadlines.
What are my options for learning more about manufacturing
Hands-on experience is the best way to learn more about manufacturing. However, if that's not possible, you can always read books or watch educational videos.
What is production management?
Production Planning refers to the development of a plan for every aspect of production. This document will ensure everything is in order and ready to go when you need it. This document should also include information on how to get the best result on set. It should include information about shooting locations, casting lists, crew details, equipment requirements, and shooting schedules.
The first step is to decide what you want. You may have decided where to shoot or even specific locations you want to use. Once you have identified your locations and scenes it's time to begin figuring out what elements you will need for each one. Perhaps you have decided that you need to buy a car but aren't sure which model. To narrow your options, you can search online for available models.
After you have chosen the right car, you will be able to begin thinking about accessories. You might need to have people in the front seats. Or perhaps you need someone walking around the back of the car? Maybe you want to change the interior color from black to white? These questions will help to determine the style and feel of your car. Also, think about what kind of shots you would like to capture. Will you be filming close-ups or wide angles? Maybe you want the engine or the steering wheels to be shown. These factors will help you determine which car style you want to film.
Once you've determined the above, it is time to start creating a calendar. The schedule will show you when to begin shooting and when to stop. A schedule for each day will detail when you should arrive at the location and when you need leave. It will help everyone know exactly what they have to do and when. You can also make sure to book extra staff in advance if you have to hire them. You should not hire anyone who doesn't show up because of your inaction.
You will need to factor in the days that you have to film when creating your schedule. Some projects can be completed in a matter of days or weeks. Others may take several days. It is important to consider whether you require more than one photo per day when you create your schedule. Multiplying takes in the same area will result both in increased costs and a longer time. If you aren't sure whether you need multiple shots, it is best to take fewer photos than you would like.
Budget setting is another important aspect in production planning. You will be able to manage your resources if you have a realistic budget. Remember that you can always reduce the budget later on if you run into unforeseen problems. But, don't underestimate how much money you'll spend. You will end up spending less money if you underestimate the cost of something.
Production planning can be a complex process. However, once you know how everything works together it will become easier to plan future projects.
What do we need to know about Manufacturing Processes in order to learn more about Logistics?
No. No. It is important to know about the manufacturing processes in order to understand how logistics works.
Statistics
- In 2021, an estimated 12.1 million Americans work in the manufacturing sector.6 (investopedia.com)
- Job #1 is delivering the ordered product according to specifications: color, size, brand, and quantity. (netsuite.com)
- According to a Statista study, U.S. businesses spent $1.63 trillion on logistics in 2019, moving goods from origin to end user through various supply chain network segments. (netsuite.com)
- In the United States, for example, manufacturing makes up 15% of the economic output. (twi-global.com)
- It's estimated that 10.8% of the U.S. GDP in 2020 was contributed to manufacturing. (investopedia.com)
External Links
How To
How to Use 5S to Increase Productivity in Manufacturing
5S stands for "Sort", 'Set In Order", 'Standardize', & Separate>. Toyota Motor Corporation invented the 5S strategy in 1954. It assists companies in improving their work environments and achieving higher efficiency.
This method has the basic goal of standardizing production processes to make them repeatable. This means that tasks such as cleaning, sorting, storing, packing, and labeling are performed daily. These actions allow workers to perform their job more efficiently, knowing what to expect.
Implementing 5S involves five steps: Sort, Set in Order, Standardize Separate, Store, and Each step involves a different action which leads to increased efficiency. For example, when you sort things, you make them easy to find later. When items are ordered, they are put together. Once you have separated your inventory into groups and organized them, you will store these groups in easily accessible containers. Finally, label all containers correctly.
This requires employees to critically evaluate how they work. Employees need to be able understand their motivations and discover alternative ways to do them. In order to use the 5S system effectively, they must be able to learn new skills.
The 5S Method not only improves efficiency, but it also helps employees to be more productive and happier. They will feel motivated to strive for higher levels of efficiency once they start to see results.