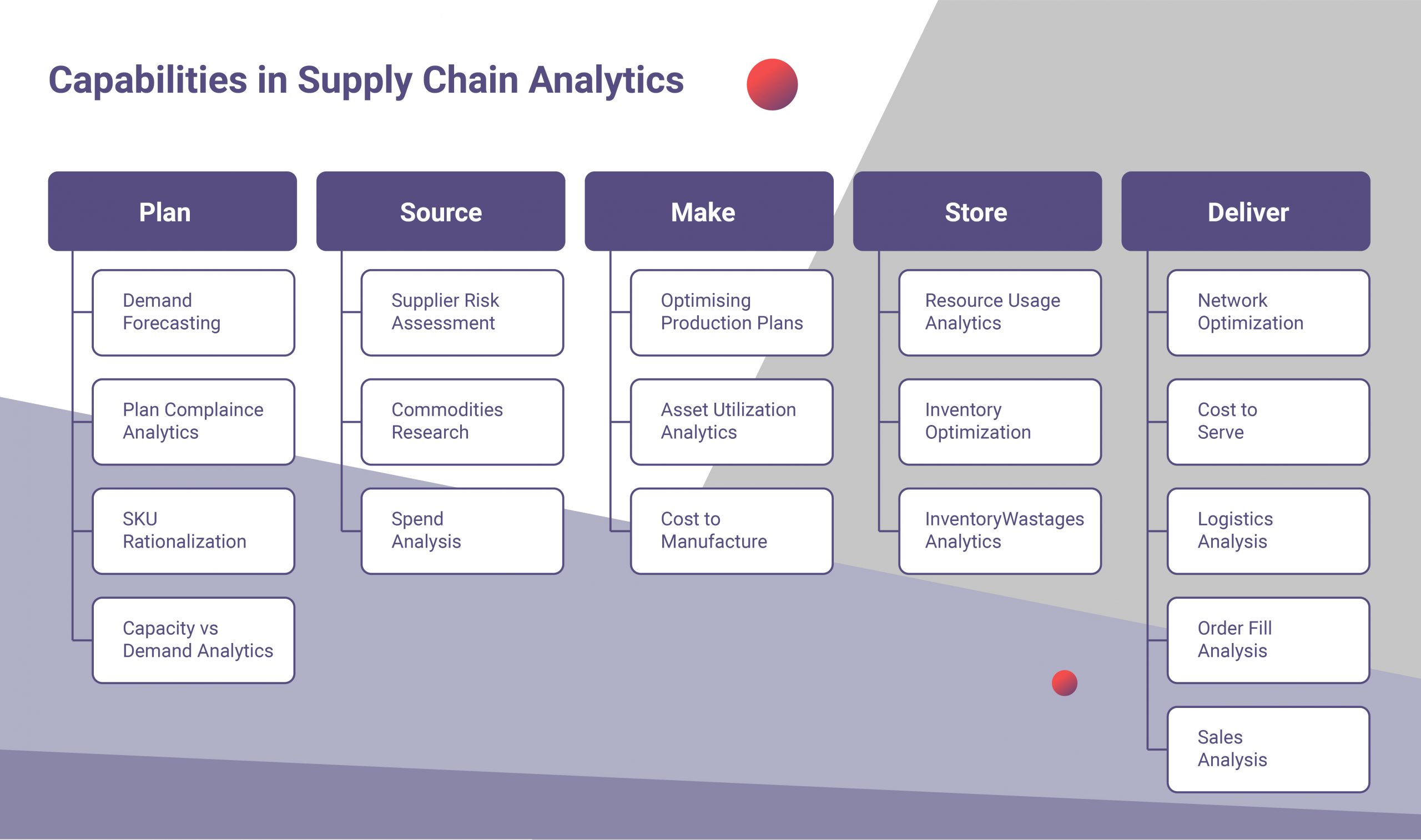
Watts didn't know he wanted to be a supply-chain major when he graduated. Jack Jensen's, managing director of Moore School's program in supply chain management, convinced Watts that the program was for him by promising him an opportunity to work with the school's capstone consultancy project.
Students can dive deep into supply-chain problems with real-world projects that companies and non-profits are working on. Jensen says that the Moore School, in partnership with 150 companies over the past eight years, has identified cost savings of more than $175,000,000 through undergraduate student projects.
During their coursework, students work closely with faculty advisors and organizations to analyze real-world supply chain issues using data science tools like Lean Manufacturing and Six Sigma. They also learn to prepare, organize, and transform data, build models, and evaluate results.
After completing the course, students complete a capstone project in which they present the problem, significance to theory and business practice, research of the project background, a well-defined method, and results or findings.
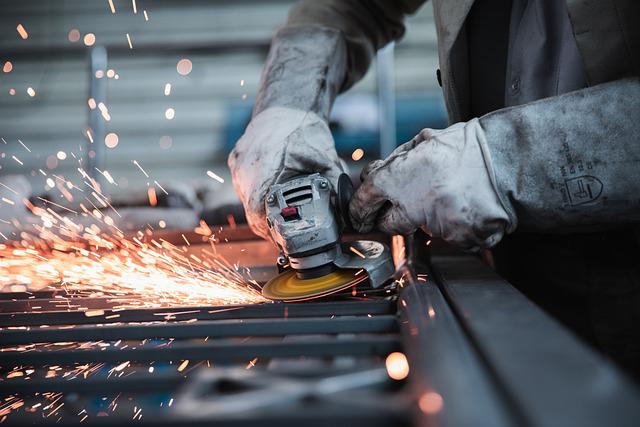
In addition to being a great opportunity to apply the knowledge and skills gained through your degree, the capstone project is a valuable learning experience and an excellent way to demonstrate your commitment to your education.
As a result, many schools offer their students the opportunity to complete a capstone project as part of their graduation requirements. These projects may be difficult and take a considerable amount of time and work to complete.
The project may be completed over the course a semester, or even longer. The project should be completed in between 100 and 120 hours.
Towson place apartment is a community of student housing located near campus. It offers studios, 1- and 2-bedroom apartments. Capstone Management offers residents a variety of amenities that are tailored to their needs.
Millennium Hall is a three building community with 400 beds that was developed by Towson in partnership and completed in 2001. The building's tenants include both undergraduate and graduate students. The complex consists of studios as well one and two bedroom units. There is also a central mailbox and a laundry facility.
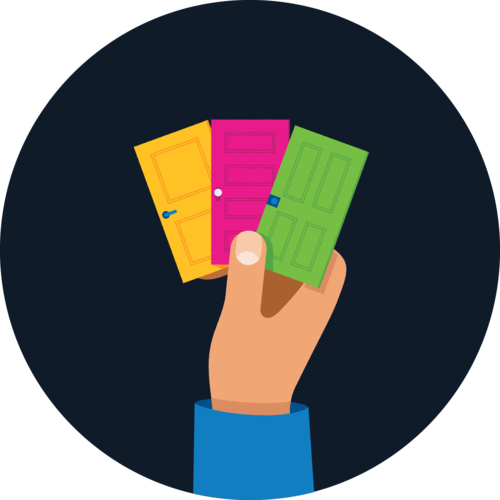
MEDCO rents out Millennium Hall as well as Paca and Tubman homes from TU. Capstone Properties Inc. manages the day-today activities for MEDCO.
Several families have sued MEDCO, claiming breach of contract. They claim that their lease agreements are holding them hostage as TU moves to distance learning. The families claim that MEDCO has refused to refund their rents and release them from their lease agreements, despite following guidelines established by TU Housing and Residence Life, the University of Maryland Campus Living Services and the Center for Disease Control.
The case was filed in March 2018 and has yet to be resolved. Lucchi's case will be pursued further after he has received responses and advice from MEDCO's lawyers.
FAQ
What kind of jobs are there in logistics?
There are many kinds of jobs available within logistics. Here are some examples:
-
Warehouse workers: They load and unload trucks, pallets, and other cargo.
-
Transportation drivers - They drive trucks and trailers to deliver goods and carry out pick-ups.
-
Freight handlers - They sort and pack freight in warehouses.
-
Inventory managers – They manage the inventory in warehouses.
-
Sales representatives: They sell products to customers.
-
Logistics coordinators – They plan and coordinate logistics operations.
-
Purchasing agents: They are responsible for purchasing goods and services to support company operations.
-
Customer service representatives - Answer calls and email from customers.
-
Ship clerks - They issue bills and process shipping orders.
-
Order fillers - They fill orders based on what is ordered and shipped.
-
Quality control inspectors: They inspect outgoing and incoming products for any defects.
-
Others - There are many types of jobs in logistics such as transport supervisors and cargo specialists.
How can manufacturing efficiency be improved?
The first step is to determine the key factors that impact production time. We then need to figure out how to improve these variables. If you don’t know how to start, look at which factors have the greatest impact upon production time. Once you have identified the factors, then try to find solutions.
How can manufacturing excess production be decreased?
In order to reduce excess production, you need to develop better inventory management methods. This would reduce the time spent on unproductive activities like purchasing, storing and maintaining excess stock. This could help us free up our time for other productive tasks.
A Kanban system is one way to achieve this. A Kanban Board is a visual display that tracks work progress. A Kanban system allows work items to move through several states before reaching their final destination. Each state represents a different priority level.
As an example, if work is progressing from one stage of the process to another, then the current task is complete and can be transferred to the next. It is possible to keep a task in the beginning stages until it gets to the end.
This keeps work moving and ensures no work is lost. A Kanban board allows managers to monitor how much work is being completed at any given moment. This data allows them adjust their workflow based upon real-time data.
Lean manufacturing is another way to manage inventory levels. Lean manufacturing is about eliminating waste from all stages of the production process. Anything that doesn't add value to the product is considered waste. There are several types of waste that you might encounter:
-
Overproduction
-
Inventory
-
Packaging that is not necessary
-
Materials in excess
These ideas can help manufacturers improve efficiency and reduce costs.
Statistics
- It's estimated that 10.8% of the U.S. GDP in 2020 was contributed to manufacturing. (investopedia.com)
- You can multiply the result by 100 to get the total percent of monthly overhead. (investopedia.com)
- Job #1 is delivering the ordered product according to specifications: color, size, brand, and quantity. (netsuite.com)
- In the United States, for example, manufacturing makes up 15% of the economic output. (twi-global.com)
- (2:04) MTO is a production technique wherein products are customized according to customer specifications, and production only starts after an order is received. (oracle.com)
External Links
How To
How to Use Just-In-Time Production
Just-intime (JIT), which is a method to minimize costs and maximize efficiency in business process, is one way. This is where you have the right resources at the right time. This means that your only pay for the resources you actually use. Frederick Taylor was the first to coin this term. He developed it while working as a foreman during the early 1900s. He saw how overtime was paid to workers for work that was delayed. He decided to ensure workers have enough time to do their jobs before starting work to improve productivity.
JIT teaches you to plan ahead and prepare everything so you don’t waste time. Look at your entire project, from start to end. Make sure you have enough resources in place to deal with any unexpected problems. You'll be prepared to handle any potential problems if you know in advance. You won't have to pay more for unnecessary items.
There are many JIT methods.
-
Demand-driven: This JIT is where you place regular orders for the parts/materials that are needed for your project. This will allow to track how much material has been used up. This will allow to you estimate the time it will take for more to be produced.
-
Inventory-based: This type allows you to stock the materials needed for your projects ahead of time. This allows you to forecast how much you will sell.
-
Project-driven : This is a method where you make sure that enough money is set aside to pay the project's cost. If you know the amount you require, you can buy the materials you need.
-
Resource-based JIT: This is the most popular form of JIT. Here you can allocate certain resources based purely on demand. You will, for example, assign more staff to deal with large orders. If you don't receive many orders, then you'll assign fewer employees to handle the load.
-
Cost-based: This is a similar approach to resource-based but you are not only concerned with how many people you have, but also how much each one costs.
-
Price-based: This approach is very similar to the cost-based method except that you don't look at individual workers costs but the total cost of the company.
-
Material-based: This approach is similar to cost-based. However, instead of looking at the total cost for the company, you look at how much you spend on average on raw materials.
-
Time-based JIT is another form of resource-based JIT. Instead of focusing only on how much each employee is costing, you should focus on how long it takes to complete your project.
-
Quality-based JIT: Another variation on resource-based JIT. Instead of thinking about how much each employee costs or how long it takes to manufacture something, you think about how good the quality of your product is.
-
Value-based JIT: One of the most recent forms of JIT. In this scenario, you're not concerned about how products perform or whether customers expect them to meet their expectations. Instead, you're focused on how much value you add to the market.
-
Stock-based. This method is inventory-based and focuses only on the actual production at any given point. This is used to increase production and minimize inventory.
-
Just-in time (JIT), planning: This is a combination JIT/supply chain management. It refers to the process of scheduling the delivery of components as soon as they are ordered. This is important as it reduces lead time and increases throughput.