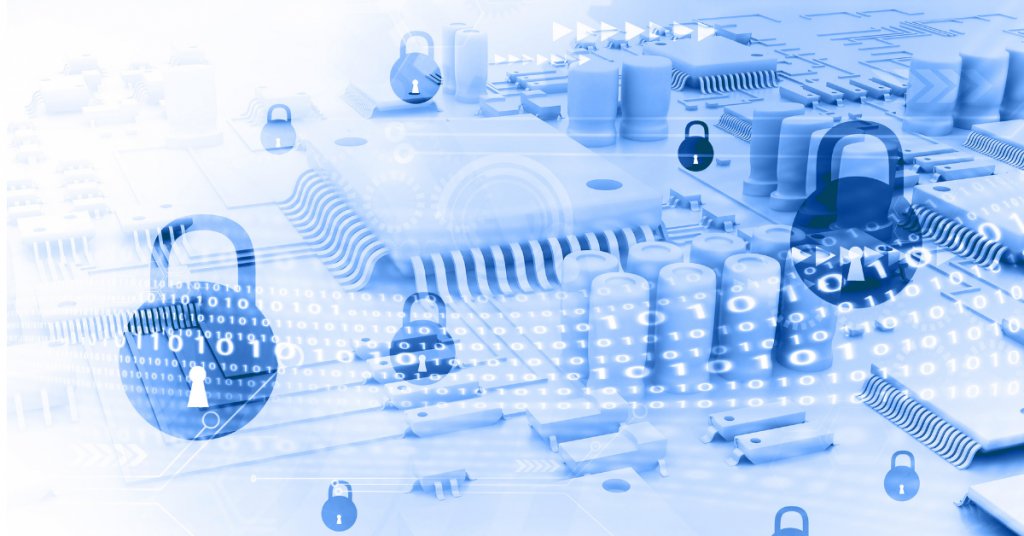
Depending on the type of product you're looking to make, there are different manufacturing processes. Manufacturing can be done by machine or manually. A manufacturing business may sell its goods to retailers, wholesalers, or consumers directly. It may also sell its goods through an online retail store.
Materials and equipment are necessary to produce a product. A manufacturing company might choose to buy materials from vendors or to produce its own. A jewelry manufacturer might purchase the materials needed to create a new bracelet. Once they have combined them, they can assemble the product using a few tools.
Some manufacturing processes require sophisticated machinery and tools. For instance, cell phones are made from raw materials, which must be combined with sophisticated tools. These products are then shipped out to the buyers.
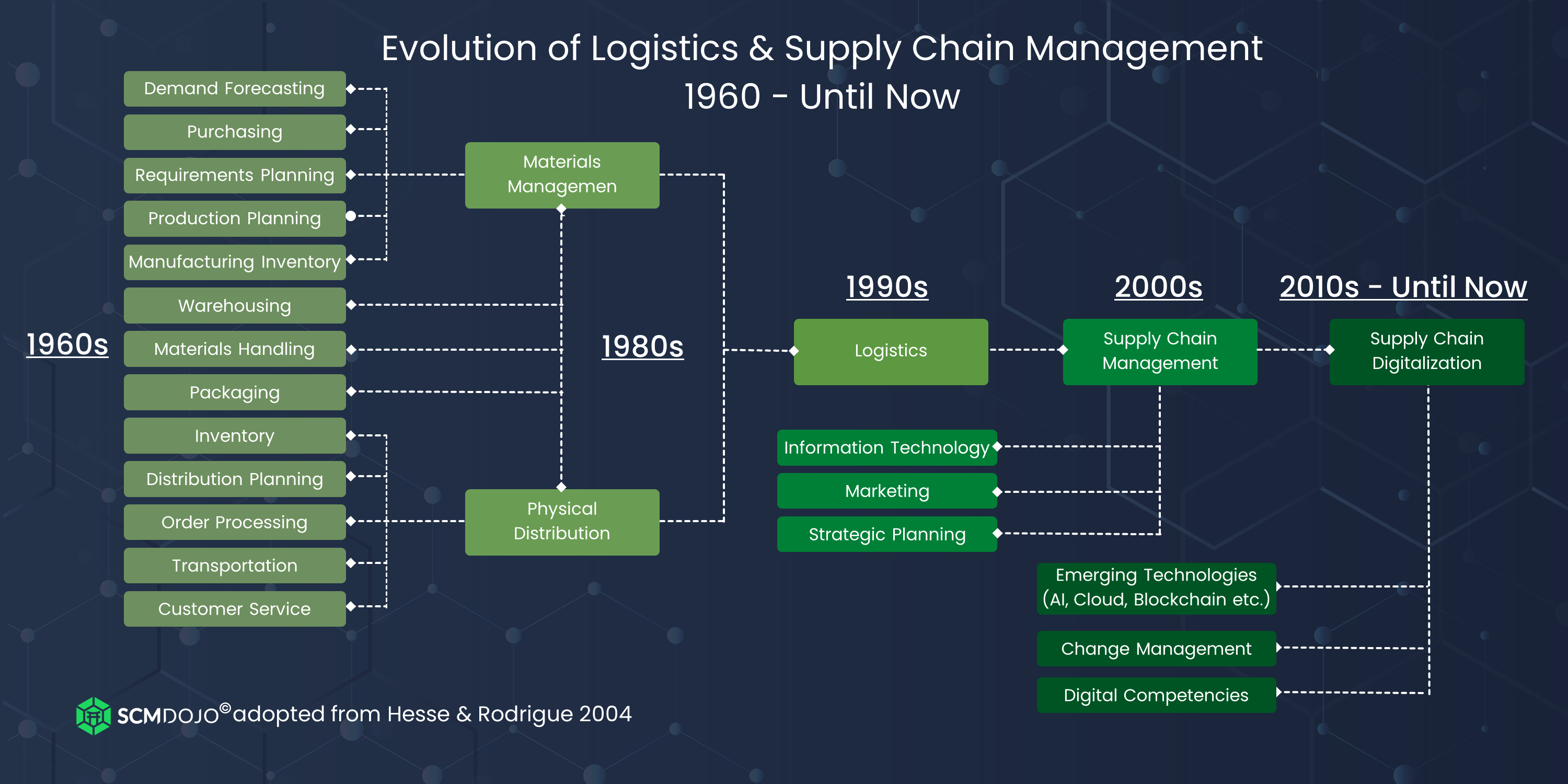
A manufacturing company may need to pay more to hire workers with more advanced skills in order to produce an advanced product. Manufacturing is a large, expensive business that can take years to grow. This type of business will likely need to save money in order to continue to thrive over the long-term. A manufacturing business may also need to hire employees as needed.
Manufacturing is an interesting career choice. Customers may have the best products, and a manufacturing company might find these items to be the most profitable. They may also find that they must produce more products with less waste. Manufacturing isn't right for everyone.
Manufacturing can be difficult, especially if your business doesn't have the right tools. Manufacturing businesses might find it difficult to find workers to work at all hours of day or to finish their work on time. This can lead to lower profits and higher costs. Manufacturing requires large investments in equipment and labor.
Manufacturing has a long history. This is one of the most important facts to understand about it. It originated thousands of year ago as an art form linked to traditional artifacts. Manufacturing is one of today's most important economic activities. Manufacturing helps industrializing nations expand their economies by providing goods for sale and employment opportunities.
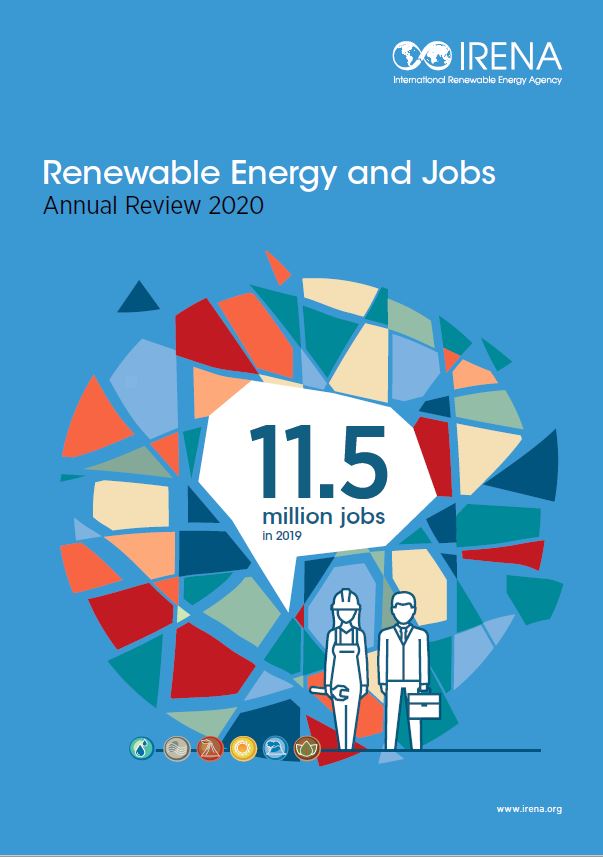
Manufacturing is much more complicated than it appears. There could be hundreds of steps. Quality control is an important part of the manufacturing process. Because it ensures that the finished product meets safety standards and protects the brand identity, quality control is essential. This is especially true if the manufacturer intends on selling its finished goods to wholesalers and consumers.
The manufacturing process may take place in virtually any location. There are many different kinds of manufacturing, but they all fall under one of three categories: process, discrete, or make to order. Each one has its strengths and weaknesses. It is essential to understand each type of manufacturing process in order to benefit your company.
FAQ
What is the job of a production plan?
A production planner ensures all aspects of the project are delivered on time, within budget, and within scope. They also ensure that the product/service meets the client’s needs.
What types of jobs can you find in logistics
There are different kinds of jobs available in logistics. Here are some examples:
-
Warehouse workers: They load and unload trucks, pallets, and other cargo.
-
Transportation drivers: They drive trucks and trailers and deliver goods and make pick-ups.
-
Freight handlers are people who sort and pack freight into warehouses.
-
Inventory managers – These people oversee inventory at warehouses.
-
Sales representatives - They sell products.
-
Logistics coordinators – They plan and coordinate logistics operations.
-
Purchasing agents are those who purchase goods and services for the company.
-
Customer service agents - They answer phone calls and respond to emails.
-
Shipping clerks: They process shipping requests and issue bills.
-
Order fillers are people who fill orders based only on what was ordered.
-
Quality control inspectors – They inspect incoming and outgoing products to ensure that there are no defects.
-
Others - There is a variety of other jobs in logistics. These include transportation supervisors and cargo specialists.
What is the role of a manager in manufacturing?
The manufacturing manager should ensure that every manufacturing process is efficient and effective. They should be aware of any issues within the company and respond accordingly.
They should also know how to communicate with other departments such as sales and marketing.
They should also be knowledgeable about the latest trends in the industry so they can use this information for productivity and efficiency improvements.
What is the difference between Production Planning, Scheduling and Production Planning?
Production Planning (PP), is the process of deciding what production needs to take place at any given time. This is done through forecasting demand and identifying production capacities.
Scheduling is the process that assigns dates to tasks so they can get completed within a given timeframe.
What are the requirements to start a logistics business?
A successful logistics business requires a lot more than just knowledge. Good communication skills are essential to effectively communicate with your suppliers and clients. You should be able analyse data and draw inferences. You must be able and able to handle stress situations and work under pressure. To improve efficiency, you must be innovative and creative. You will need strong leadership skills to motivate and direct your team members towards achieving their organizational goals.
You must be organized to meet tight deadlines.
Statistics
- (2:04) MTO is a production technique wherein products are customized according to customer specifications, and production only starts after an order is received. (oracle.com)
- You can multiply the result by 100 to get the total percent of monthly overhead. (investopedia.com)
- In 2021, an estimated 12.1 million Americans work in the manufacturing sector.6 (investopedia.com)
- According to the United Nations Industrial Development Organization (UNIDO), China is the top manufacturer worldwide by 2019 output, producing 28.7% of the total global manufacturing output, followed by the United States, Japan, Germany, and India.[52][53] (en.wikipedia.org)
- According to a Statista study, U.S. businesses spent $1.63 trillion on logistics in 2019, moving goods from origin to end user through various supply chain network segments. (netsuite.com)
External Links
How To
Six Sigma: How to Use it in Manufacturing
Six Sigma is defined by "the application SPC (statistical process control) techniques to achieve continuous improvements." Motorola's Quality Improvement Department in Tokyo, Japan developed Six Sigma in 1986. The basic idea behind Six Sigma is to improve quality by improving processes through standardization and eliminating defects. Since there are no perfect products, or services, this approach has been adopted by many companies over the years. Six Sigma's primary goal is to reduce variation from the average value of production. If you take a sample and compare it with the average, you will be able to determine how much of the production process is different from the norm. If this deviation is too big, you know something needs fixing.
The first step toward implementing Six Sigma is understanding how variability works in your business. Once you have this understanding, you will need to identify sources and causes of variation. It is important to identify whether the variations are random or systemic. Random variations are caused when people make mistakes. While systematic variations are caused outside of the process, they can occur. These are, for instance, random variations that occur when widgets are made and some fall off the production line. But if you notice that every widget you make falls apart at the exact same place each time, this would indicate that there is a problem.
Once you've identified the problem areas you need to find solutions. This could mean changing your approach or redesigning the entire process. After implementing the new changes, you should test them again to see if they worked. If they didn't work, then you'll need to go back to the drawing board and come up with another plan.