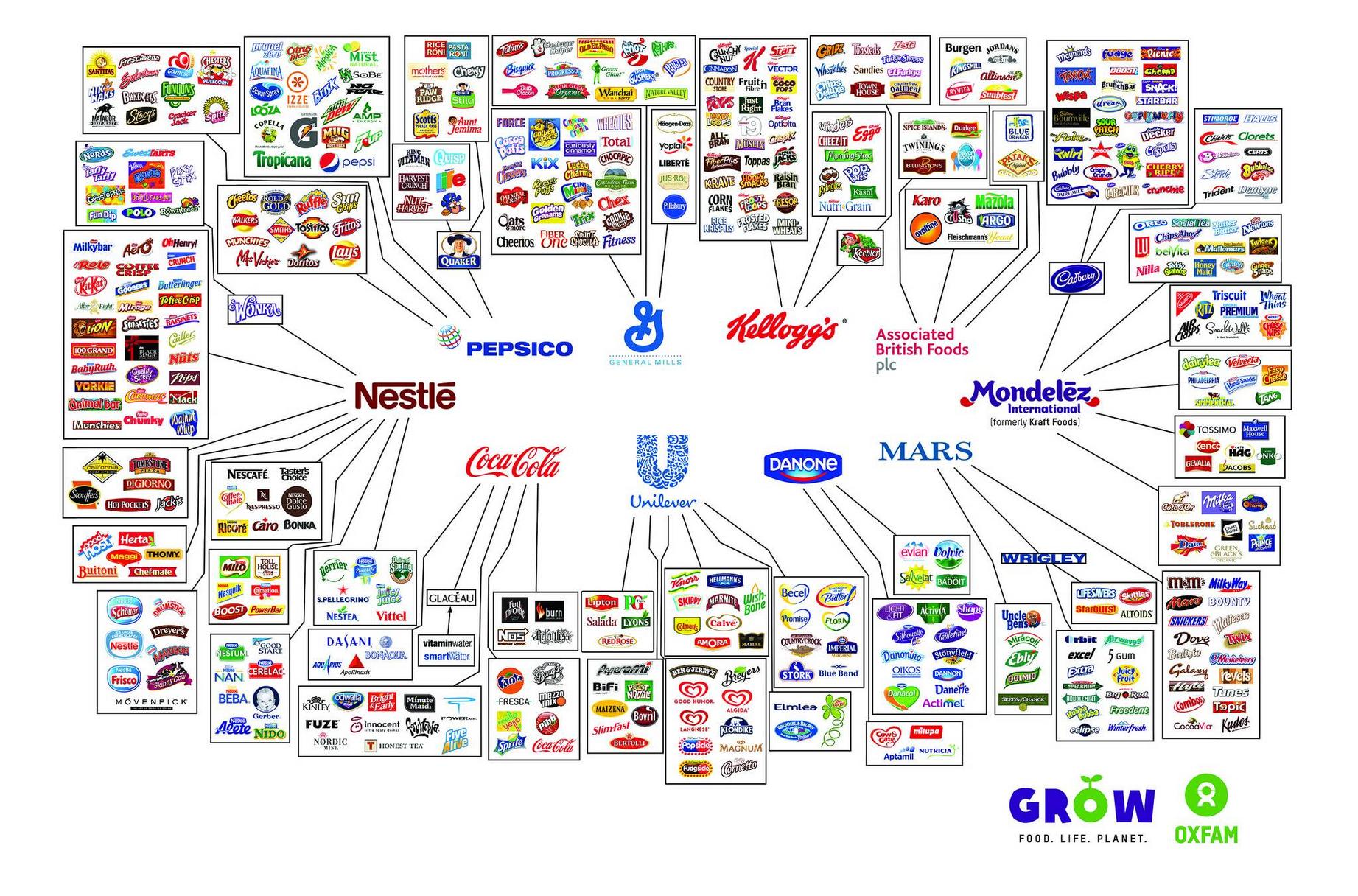
The job of a logistics coordinator involves ensuring that goods are in the right place at the right time and arrive in the most efficient and cost-effective way possible. In this field, you'll ensure that goods are delivered efficiently to your customer's door. Find out more about logistics by reading our article. We will also discuss the roles of customer service specialists, inventory analysts, and supply chain managers. Listed below are some of the top jobs that you can find in logistics.
Logistics coordinator
If you want to start a career as a logistics coordinator, you can find thousands of jobs on Monster. This type of job requires a lot of hands-on training. Candidates who have little or no industry experience will be expected to complete the apprenticeship or internship. If you have prior experience in the logistics industry, you might be interested to apply for a job with Logistics Coordinator.
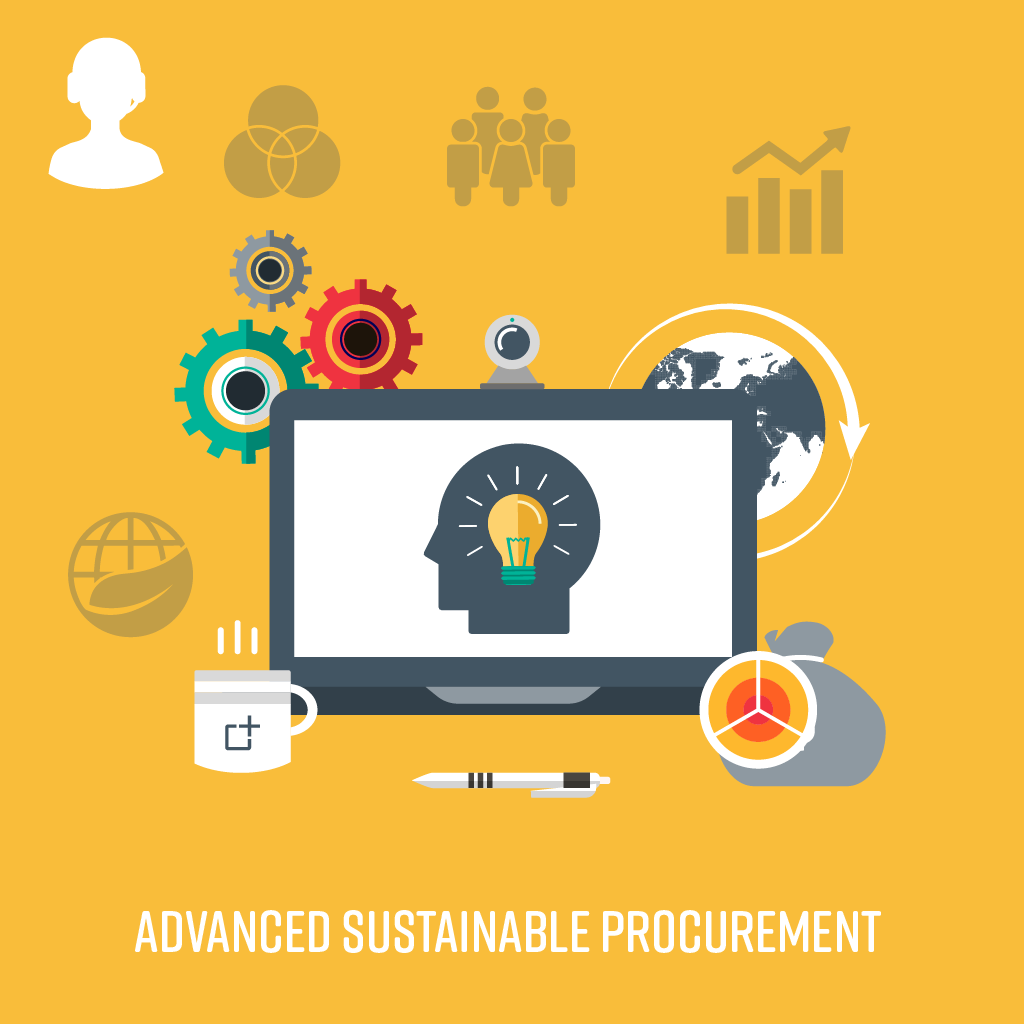
Customer service specialist
A customer service specialist oversees the delivery and management of customer service. They work with customers to communicate daily, coordinate inland shipping, and resolve customer problems and complaints. In addition to managing customer relationships, they also coordinate appointments, document special service needs, and schedule transportation and warehousing processes. As a customer service specialist, you will also coordinate and document all necessary documents to ensure the delivery of goods on time and within budget.
Inventory analyst
An Inventory Analyst manages inventory productivity and maintains service level. They are responsible for the fulfillment of all orders for TSC Feed programs and the management of the daily activities associated with inventory replenishment. They manage the inventory levels of their product categories and support assortment and merchandise plan. They use data to analyze trends and plan article-site replenishment. They may also assist with marketing and promotional activities. They are often in charge of analyzing sales data and creating new strategies to enhance business efficiency.
Supply chain manager
The role of a supply chain manager involves managing the flow and movement of materials from suppliers to manufacturers and customers. This role requires a broad range of skills. Typically, a bachelor's degree in business administration is required. Many employers prefer candidates who have a master's in business administration. There are many options to get a job as a supply chain manager. Find out more about this career field. If you're thinking of going into supply chain management, consider getting an associate's degree in business administration first.
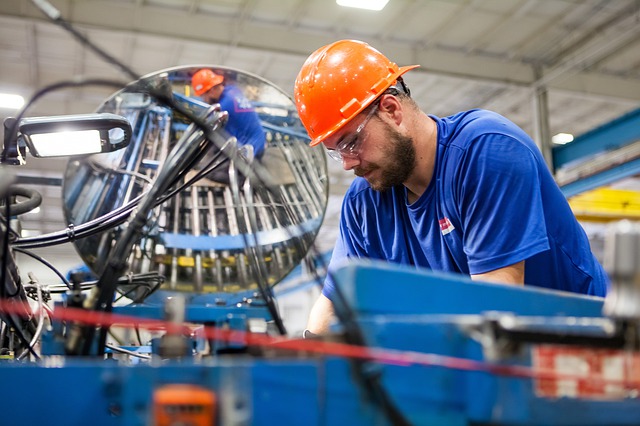
Freight agent
Your cargo and freight agent responsibilities should be included in your job description. So that potential candidates can see what they have to do every day, the job description should include a list of key responsibilities. Make sure to use strong action verbs in your description to get the attention of qualified applicants. It is important to include in the job description a list detailing all qualifications needed for this position.
FAQ
What does manufacturing industry mean?
Manufacturing Industries is a group of businesses that produce goods for sale. Consumers are people who purchase these goods. These companies use a variety processes such as distribution, retailing and management to accomplish their purpose. They make goods from raw materials with machines and other equipment. This includes all types of manufactured goods, including food items, clothing, building supplies, furniture, toys, electronics, tools, machinery, vehicles, pharmaceuticals, medical devices, chemicals, and many others.
What are the jobs in logistics?
There are many types of jobs in logistics. Some of them are:
-
Warehouse workers – They load and unload pallets and trucks.
-
Transport drivers - These are people who drive trucks and trailers to transport goods or perform pick-ups.
-
Freight handlers – They sort and package freight at warehouses.
-
Inventory managers – They manage the inventory in warehouses.
-
Sales reps are people who sell products to customers.
-
Logistics coordinators are responsible for organizing and planning logistics operations.
-
Purchasing agents - They buy goods and services that are necessary for company operations.
-
Customer service representatives are available to answer customer calls and emails.
-
Shippers clerks - They process shipping order and issue bills.
-
Order fillers are people who fill orders based only on what was ordered.
-
Quality control inspectors – They inspect incoming and outgoing products to ensure that there are no defects.
-
Others - There is a variety of other jobs in logistics. These include transportation supervisors and cargo specialists.
How can efficiency in manufacturing be improved?
First, identify the factors that affect production time. We must then find ways that we can improve these factors. You can start by identifying the most important factors that impact production time. Once you have identified the factors, then try to find solutions.
What is it like to manage a logistics company?
To run a successful logistics company, you need a lot knowledge and skills. Good communication skills are essential to effectively communicate with your suppliers and clients. You should be able analyse data and draw inferences. You must be able manage stress and pressure under pressure. You need to be innovative and creative to come up with new ways to increase efficiency. To motivate and guide your team towards reaching organizational goals, you must have strong leadership skills.
It is also important to be efficient and well organized in order meet deadlines.
Statistics
- According to the United Nations Industrial Development Organization (UNIDO), China is the top manufacturer worldwide by 2019 output, producing 28.7% of the total global manufacturing output, followed by the United States, Japan, Germany, and India.[52][53] (en.wikipedia.org)
- [54][55] These are the top 50 countries by the total value of manufacturing output in US dollars for its noted year according to World Bank.[56] (en.wikipedia.org)
- According to a Statista study, U.S. businesses spent $1.63 trillion on logistics in 2019, moving goods from origin to end user through various supply chain network segments. (netsuite.com)
- In the United States, for example, manufacturing makes up 15% of the economic output. (twi-global.com)
- (2:04) MTO is a production technique wherein products are customized according to customer specifications, and production only starts after an order is received. (oracle.com)
External Links
How To
How to Use Just-In-Time Production
Just-in-time is a way to cut costs and increase efficiency in business processes. It is a process where you get the right amount of resources at the right moment when they are needed. This means that you only pay for what you actually use. Frederick Taylor was the first to coin this term. He developed it while working as a foreman during the early 1900s. He saw how overtime was paid to workers for work that was delayed. He decided that workers would be more productive if they had enough time to complete their work before they started to work.
JIT is about planning ahead. You should have all the necessary resources ready to go so that you don’t waste money. The entire project should be looked at from start to finish. You need to ensure you have enough resources to tackle any issues that might arise. You will have the resources and people to solve any problems you anticipate. You won't have to pay more for unnecessary items.
There are many JIT methods.
-
Demand-driven JIT: This is a JIT that allows you to regularly order the parts/materials necessary for your project. This will allow to track how much material has been used up. It will also allow you to predict how long it takes to produce more.
-
Inventory-based: You stock materials in advance to make your projects easier. This allows one to predict how much they will sell.
-
Project-driven: This method allows you to set aside enough funds for your project. You will be able to purchase the right amount of materials if you know what you need.
-
Resource-based: This is the most common form of JIT. You allocate resources based on the demand. You will, for example, assign more staff to deal with large orders. If you don't have many orders, you'll assign fewer people to handle the workload.
-
Cost-based: This is the same as resource-based except that you don't care how many people there are but how much each one of them costs.
-
Price-based: This is very similar to cost-based, except that instead of looking at how much each individual worker costs, you look at the overall price of the company.
-
Material-based: This approach is similar to cost-based. However, instead of looking at the total cost for the company, you look at how much you spend on average on raw materials.
-
Time-based JIT: A variation on resource-based JIT. Instead of focusing on the cost of each employee, you will focus on the time it takes to complete a project.
-
Quality-based JIT is another variant of resource-based JIT. Instead of worrying about the costs of each employee or how long it takes for something to be made, you should think about how quality your product is.
-
Value-based: This is one of the newest forms of JIT. This is where you don't care about how the products perform or whether they meet customers' expectations. Instead, you focus on the added value that you provide to your market.
-
Stock-based. This method is inventory-based and focuses only on the actual production at any given point. This method is useful when you want to increase production while decreasing inventory.
-
Just-in-time (JIT) planning: This is a combination of JIT and supply chain management. This refers to the scheduling of the delivery of components as soon after they are ordered. This is important as it reduces lead time and increases throughput.