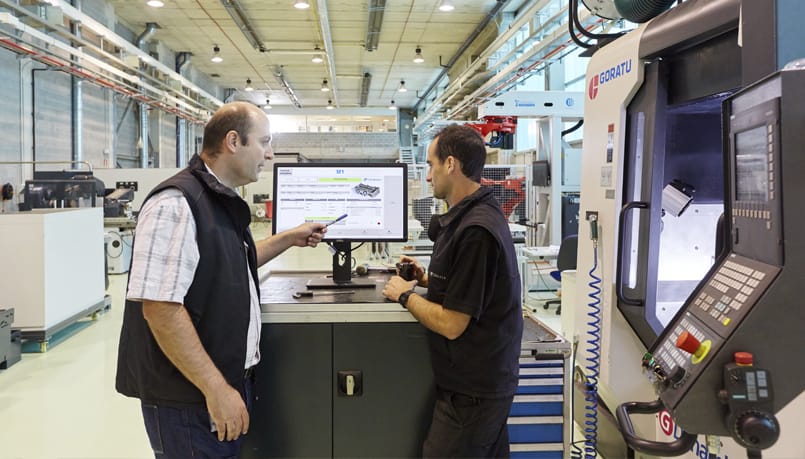
The United States is the third largest country manufacturer in the entire world. Its manufacturing output was almost double that of the Great Recession. Despite having a strong national economy, the United States’ manufacturing industry is taking a very aggressive approach to its current challenges. This could be due to a shortage of skilled labor or investment, but we must be more aggressive in dealing with the problems facing our industry.
Since 2000, 5 million fewer jobs have been created.
Five million US manufacturing jobs have been lost since 2000. Some people blame the rise in trade with China, but that accounts only for about a fourth the decline in manufacturing jobs. In addition to trade with China, manufacturing jobs were lost in local markets that didn't compete with Chinese imports. But the reasons for the decline in manufacturing jobs are many. The following are some of the reasons:
During the last two decades, the US manufacturing sector lost nearly a third of its jobs. It was at 17 million in 1965 and dropped to a mere 12 million in 2010. Trade is not responsible for the decline in manufacturing jobs. However, it has been caused structural problems like a decline of capital investment, output, and productivity. These problems are not sustainable. Although productivity gains had a large role in the decline in manufacturing jobs, they weren't enough. Not productivity gains, but automation is the problem.
The demand for manufactured products is strong
The demand for manufactured goods in the United States remains strong, despite the fact the percentage of consumers spending on them has declined over the last few decades. In 1945 personal spending on durable goods accounted 58% of total spending. Today, it accounts for only 28%. This is because the cost of manufacturing and sale of these goods has dropped while the content has increased. Computers, televisions, sound equipment, and other electronic devices have seen significant drops in their prices.
The US's recovery in manufacturing activity has resulted in an increase in the production of manufactured goods. The Fifth District Manufacturing Activity Survey reveals that the demand for manufactured products is strong, with production increasing rapidly. However, supply chain problems are slowing down output. The increased production has put stress on supply chains, and respondents have reported supply chain disruptions that affect their ability to maintain necessary inventories. Backlogs in orders have increased and so has the time it takes for vendors to respond.
Trade deficit in manufactured goods has more than doubled in the past decade
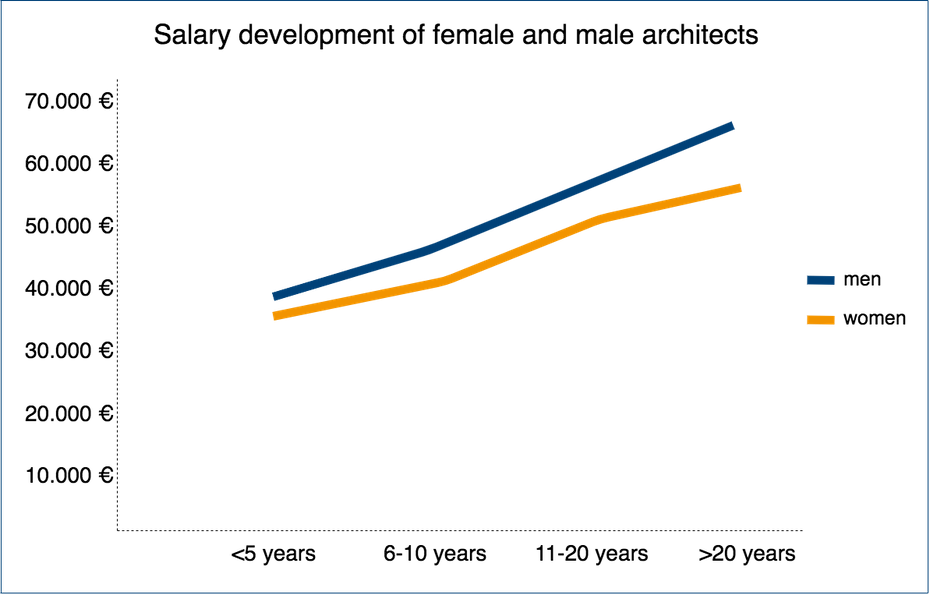
Economists are concerned that the U.S. trade surplus could lead to lower global growth and more instability among its trading partners. Some argue that the high imports of manufactured goods from the United States are not necessarily bad for its economy. This is essential to maintaining global economic stability. A trade deficit might even be necessary, as the U.S. heavily relies on foreign markets for its economic output. However, high levels of foreign demand could make it more difficult to reach full employment.
Since 2000, nearly two-thirds of the U.S. manufacturing goods trade deficit has increased. The US deficit has been growing partly because of the increase in Chinese imports. But the larger problem is that this imbalance is concentrated in the manufacturing sector, where wages and employment have decreased since the 1990s. US manufacturing jobs have dropped from 26 to 8.5 per cent in 1970, to just 6.5 percent in 2016. Some economists attribute China's increasing competition to the decline, but most blame the decline on automation, productivity increases and the shifting of consumer demand away form goods to services.
The shotgun approach of industry is the best.
The US manufacturing sector is well-known for its many advanced manufacturing initiatives. Some countries, however, are taking a more focused approach to bringing the internet into manufacturing. The US, however, is a multi-technology nation that combines traditional mass media with Internet advertising. The result is a shotgun approach. Companies focus on many technologies and target a broad client base.
FAQ
What skills does a production planner need?
Production planners must be flexible, organized, and able handle multiple tasks. You must also be able to communicate effectively with clients and colleagues.
Do we need to know about Manufacturing Processes before learning about Logistics?
No. No. However, knowing about manufacturing processes will definitely give you a better understanding of how logistics works.
Is it possible to automate certain parts of manufacturing
Yes! Yes. Automation has been around since ancient time. The wheel was invented by the Egyptians thousands of years ago. Robots are now used to assist us in assembly lines.
Robotics is used in many manufacturing processes today. They include:
-
Robots for assembly line
-
Robot welding
-
Robot painting
-
Robotics inspection
-
Robots that make products
Automation could also be used to improve manufacturing. For instance, 3D printing allows us make custom products and not have to wait for months or even weeks to get them made.
How can I find out more about manufacturing?
Practical experience is the best way of learning about manufacturing. If that is not possible, you could always read books or view educational videos.
What jobs are available in logistics?
There are many kinds of jobs available within logistics. These are some of the jobs available in logistics:
-
Warehouse workers - They load trucks and pallets.
-
Transportation drivers: They drive trucks and trailers and deliver goods and make pick-ups.
-
Freight handlers – They sort and package freight at warehouses.
-
Inventory managers - They oversee the inventory of goods in warehouses.
-
Sales representatives - They sell products to customers.
-
Logistics coordinators are responsible for organizing and planning logistics operations.
-
Purchasing agents - They purchase goods and services needed for company operations.
-
Customer service representatives – They answer emails and phone calls from customers.
-
Shipping clerks - They process shipping orders and issue bills.
-
Order fillers - They fill orders based on what is ordered and shipped.
-
Quality control inspectors - They check incoming and outgoing products for defects.
-
Others - There are many other types of jobs available in logistics, such as transportation supervisors, cargo specialists, etc.
Statistics
- In 2021, an estimated 12.1 million Americans work in the manufacturing sector.6 (investopedia.com)
- (2:04) MTO is a production technique wherein products are customized according to customer specifications, and production only starts after an order is received. (oracle.com)
- Job #1 is delivering the ordered product according to specifications: color, size, brand, and quantity. (netsuite.com)
- According to the United Nations Industrial Development Organization (UNIDO), China is the top manufacturer worldwide by 2019 output, producing 28.7% of the total global manufacturing output, followed by the United States, Japan, Germany, and India.[52][53] (en.wikipedia.org)
- Many factories witnessed a 30% increase in output due to the shift to electric motors. (en.wikipedia.org)
External Links
How To
Six Sigma in Manufacturing:
Six Sigma can be described as "the use of statistical process control (SPC), techniques to achieve continuous improvement." Motorola's Quality Improvement Department in Tokyo, Japan developed Six Sigma in 1986. Six Sigma's core idea is to improve the quality of processes by standardizing and eliminating defects. Many companies have adopted Six Sigma in recent years because they believe that there are no perfect products and services. Six Sigma's primary goal is to reduce variation from the average value of production. It is possible to measure the performance of your product against an average and find the percentage of time that it differs from the norm. If the deviation is excessive, it's likely that something needs to be fixed.
Understanding how variability works in your company is the first step to Six Sigma. Once you've understood that, you'll want to identify sources of variation. Also, you will need to identify the sources of variation. Random variations happen when people make errors; systematic variations are caused externally. For example, if you're making widgets, and some of them fall off the assembly line, those would be considered random variations. But if you notice that every widget you make falls apart at the exact same place each time, this would indicate that there is a problem.
Once you identify the problem areas, it is time to create solutions. It might mean changing the way you do business or redesigning it entirely. To verify that the changes have worked, you need to test them again. If they don’t work, you’ll need to go back and rework the plan.